Full analysis of air conditioning automatic control system
1. Which parts of the central air-conditioning system need to be equipped with automatic control?
Answer: It mainly includes two parts: the host part of the cold and heat source and the end equipment part, which need to be equipped with automatic control systems.
2. What is the function of the automatic control system of the terminal equipment?
Answer: The role of the control system is nothing more than a few points:
(1) The temperature, humidity, pressure, etc. of the air-conditioning area are controlled. For comfort air-conditioning, the temperature and humidity are too high or too low, which will affect the comfort. Only automatic control can automatically control the temperature and humidity at the design value; for process air-conditioning, it is the production process Prerequisites.
(2) Equipment protection, automatic maintenance, etc., such as the differential pressure alarm of the filter, prompting to clean the clogged filter in time, and the interlocking control of the fan and the heater, the wind is turned off, the heater must be automatically turned off, otherwise it may cause Fire etc.
(3) It has the effect of energy saving. For example, adjusting the fan speed through frequency conversion according to the load change can reduce the energy consumption of the fan; automatically opening the new air volume in the transition season can save the energy consumption of the main engine.
3. Why do end devices such as the cold and heat source host with its own control panel need to be equipped with additional control systems?
Answer: The cold and heat source host device itself does have a control panel, but it can only protect and control the machine, and cannot solve the unified coordination problem of peripheral chilled water pumps, cooling water pumps, cooling towers, pipeline valves, etc., without additional configuration In the case of the control system, these devices had to be started and stopped manually.
In addition, the control panel of the cold and heat source host device itself cannot solve the coordination problem between multiple hosts. For example, the host that should be switched on and off is automatically selected according to the cooling and heating load, so the cooling and heating source host part of the central air conditioning system usually needs to be configured Additional automatic control system.
4. What is the upper computer and the lower computer?
Answer: The host computer refers to a computer that can directly issue control commands, usually a PC, and displays various signal changes (hydraulic pressure, water level, temperature, etc.) on the screen. The lower computer is a computer that directly controls the equipment to obtain the status of the equipment, usually PLC/SCM.
The command issued by the upper computer is first sent to the lower computer, and the lower computer interprets this command into the corresponding timing signal to directly control the corresponding equipment. The lower computer reads the device status data (generally analog) from time to time, and converts it into a digital signal and feeds it back to the upper computer.
Both upper and lower computers need programming, and both have a special development system. Conceptually, the controller and the service provider are the upper computer, and the controlled and the served are the lower computer, which can also be understood as the relationship between the host and the slave, but the upper computer and the lower computer can be converted.
5. How to configure the automatic control system?
Answer: All automatic control systems are composed of three types of equipment:
Sensors-such as temperature sensors and humidity sensors, used to convert parameters such as temperature and humidity into electrical signals for easy input into the controller, which is equivalent to human eyes, ears and other information organs.
Controller-such as DDC (Direct Digital Controller), all logic and control strategies are completed here, equivalent to the human brain.
Actuator-such as electric control valve, etc., receive commands from the controller, and adjust the parameters by changing the output of the controlled object. For example, the electric control valve can be opened to increase the flow of cold water into the surface cooler and reduce the air supply temperature. .
How to configure the automatic control system? In almost all application types with air conditioning automatic control, the above three types of equipment that need to be configured are listed, and the control principle description is given. Find the type you need to complete the automatic control system configuration.
6. What is the difference between DDC and conventional temperature and humidity controllers?
Answer: The most important difference is:
(1) DDC can be re-developed, that is, it can be programmed to change its functions, and it can be applied to any occasion of automatic control of air-conditioning. However, the functions of conventional temperature and humidity controllers are dead and will not change the control program.
(2) It has the function of remote communication to form a network.
(3) It can also expand applications. For example, if the number of points is not enough, you can connect the expansion module, or even connect the touch screen, etc., use one touch screen to connect multiple DDCs to make an economical networked monitoring.
7. Why is network monitoring sometimes needed?
Answer: If the air-conditioning system is large, the terminal equipment is numerous and scattered, and the maintenance of the control system, such as parameter setting, which air-conditioning unit needs to increase the set temperature by 1℃, it needs to be set on the on-site controller. Convenience.
If you connect all the controllers to one or more computers through the network, that is, add a host computer, you can manage all the controllers through the computer, remotely monitor the field parameters and the operating status of the equipment, and you can set the parameters remotely , It is very convenient to record historical data, fault monitoring, automatic alarm, etc. This is the benefit of network monitoring.
8. What is a point table?
Answer: In addition to some simple control systems, the formal control system design should make a point table:
Point table description:
(1) Four types of control variables are listed horizontally:
·DI――digital input, such as switch state, alarm state, etc. All variables with only 0 and 1 states;
· AI――Analog input, such as temperature, pressure and other continuously changing parameters;
· DO――Digital output, used for the control of switching equipment, such as the start and stop of the motor, the opening and closing of the butterfly valve, etc.;
·AO――Analog output, used for the control of continuously adjusted equipment, such as electric control valves, frequency converters, etc., which can smoothly adjust from fully open to fully closed.
(2) Listed vertically are the controlled objects: such as the host, terminal equipment, etc.
(3) The point table is the most important basis for configuring control equipment. For example, there are 3 AIs in total, and three different sensors, such as temperature, humidity, and pressure sensors, may need to be configured; if there are 4 AOs, four may need to be configured. AO type actuators, such as electric control valves, electric humidifiers, etc.
(4)The point table is also the most important basis for configuring the DDC controller. For example, after statistics, there are 3 AI points, 4 AO points, 6 DO points, and 8 DI points. Then it needs to be based on these four control variables. When choosing a DDC controller, it is necessary to ensure that the number of points of the various control variables of the DDC is greater than or equal to the required number of points. For example, like this example, a DDC with only 6 DIs cannot be selected. That is, the DDC itself has too many points, causing waste, too few, and not enough.
(5)9. Is DDC complicated and easy to use?
(6)
(7) Answer: DDC is now highly intelligent after long-term development. It must have at least the following functions, otherwise it is not a real DDC controller:
(8)
(9)(1) As mentioned earlier, if the AI of the DDC is enough, and the DI is exactly one less, it cannot be used. It would be great if AI and DI can be converted to each other, so the current DDC must have the function of port variable conversion, the user can choose It's much more convenient when you type.
(10)
(11)(2) There are many types of AI sensors that need to be connected to DDC, such as 0-10VDC voltage type, 4-20mA current type, PT1000 platinum resistance, NTC10K semiconductor resistance, etc. It is best to connect. Moreover, each port can be flexibly defined, so that DDC is convenient to use, and any sensor can be connected to it. Another problem is that the range can be set flexibly, and the versatility is stronger.
(12)
(13)(3) DDC needs to be programmed and should be equipped with corresponding programming software. It is best to be simple and easy to use. If you want to program from scratch, it is too difficult, so good DDC is programmed in dialog box or graphical form . For example: the electric valve must enter the regulation state when the fan is already turned on, then a simple logic should be compiled: first set up a regulation loop: which is the measurement channel AI.
(14)
(15)For example, AI5, which is the output channel AO, such as AO3, and which control strategy to choose, such as PI proportional integral control; also choose the set value, etc., and finally interlock with the fan status signal such as DI3 In one click, the entire programming is completed. Use the computer to download it to the DDC via the data cable.
(16)
(17) (4) A good DDC can also be programmed through the small keyboard that comes with it, so that the control logic can be modified without a computer.
(18)
(19) (5) If the DDC has been connected to the control network, that is, networked monitoring, the program should be able to be downloaded remotely via the network.
(20)
(21) So in general, DDC is a highly intelligent thing. Good DDC programming is not only easy, but also fun, far from comparable to ordinary controllers.
10. Regarding the controller, there are PLC and DDC. Which one should I choose?
Answer: The control system can be divided into two types according to different applications:
Industrial automatic control and building automatic control. In industrial automatic control, PLC is often used to realize process control or numerical control equipment control, while in building control, DDC is often used to realize automatic control of building electrical equipment.
For example, air conditioning system, water supply and drainage system, lighting system, power supply and distribution system, etc. DDC is the abbreviation of Direct Digital Controller (Direct Digital Controller), which is developed from PLC. Compared with PLC programmable controller, there are The following features:
·PLC is more versatile, programmable and has high control precision.
·PLC application level depends on the programmer's familiarity with the process or equipment.
· DDC has better cost performance for air-conditioning automatic control.
·DDC" solidifies a large number of control programs, such as enthalpy control, fresh air compensation control, etc. Almost all common air conditioning control requirements have ready-made programs, which greatly reduces the workload of programming and debugging.
·DDC has a standing display interface, which is easier to use and maintain.
Therefore, in the world, air-conditioning automatic control usually adopts DDC controller. However, many experienced air-conditioning energy-saving companies also use PLC, but this requires more HVAC expertise and on-site debugging capabilities and time.
Full analysis of air conditioning automatic control system<br></br>
Recent related posts
08/04/2020
Full analysis of air conditioning automatic control system<br></br>
Which parts of the central air-conditioning system need to be equipped with automatic control?<br></br> Answer: It mainly includes two parts: the host part of the cold and heat source and the end equipment part, which need to be equipped with automatic control systems
08/04/2020
Application of energy meter in air conditioning measurement<br></br>
Central air-conditioning household metering technology is more and more commonly used in public buildings with centralized cooling.
08/04/2020
Anatomy of the pressure adjustment mode of the condenser of the small chiller
During the operation of a small chiller, changes in temperature will cause changes in condensing pressure.
08/04/2020
Analysis of five major problems in current heating management
With the development of society and the continuous improvement of people's living standards, traditional heating methods and management models have become less and less suitable for the development of the times.
08/04/2020
An article clarifies the pros and cons and installation of central air conditioning
Multi-connection is what we call central air conditioning. One external unit can be connected to multiple internal units. One external unit with two internal units is called "one for two", even three is called "one for three", and so on.
08/03/2020
Why the cooling effect of central air conditioning is not ideal
Many users will encounter this situation. When the central air conditioner is turned on in the summer, the effect is acceptable.
08/03/2020
Why the cold storage project can quickly return to temperature after power failure
Recently, many people have asked why the cold storage project has a rapid constant temperature after a power failure. This problem is believed to occur when many users use the cold storage.
08/03/2020
Why do air conditioners, refrigerators, washing machines, etc. use three-wire plugs
Three-wire plug: neutral wire, live wire, ground wire. The ground wire belongs to the type of leakage protection! High-power electrical products are protected by three-phase plugs
08/03/2020
What is the key to solving the heat dissipation problem of the condenser
In the field of medical equipment, no matter what kind of equipment, users should pay attention to the maintenance and maintenance of each part after using it for a period of time.
08/03/2020
What is the difference between an air source heat pump and a heating and cooling air conditioner
According to statistics, in 2017, a total of 5.78 million households were converted from coal to electricity and gas, and 3.94 million households were completed in 28 cities in Beijing-Tianjin-Hebei and surrounding areas.
Customers frequently viewed

IWAYA DENKI Water Pump 25CJT0752
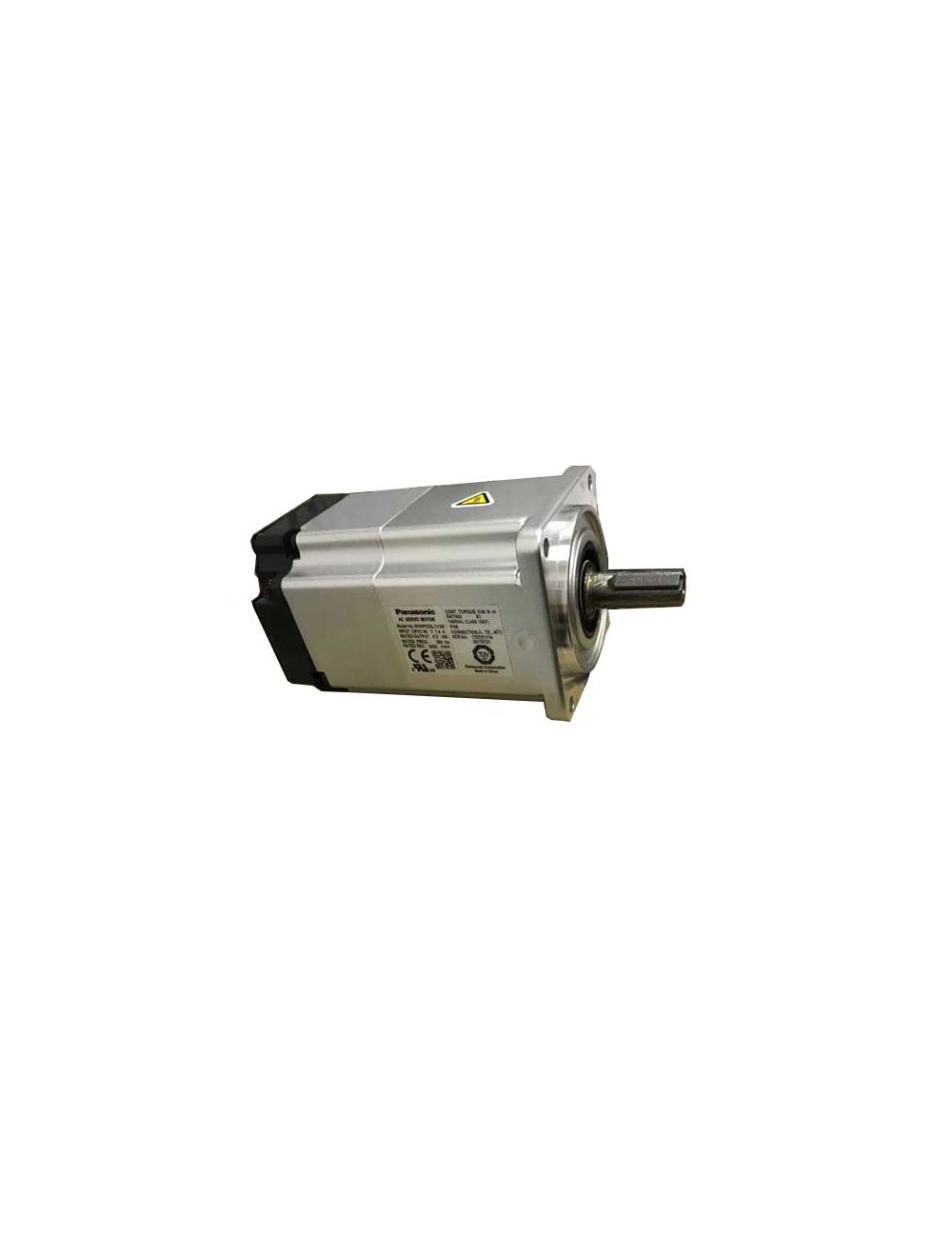
Panasonic Servo Motor MHMF022L1V2M

Honeywell Solenoid Valve VE4025B1045

ROTEN Mechanical Seal 8E5K-22-X

ADDA Fan AB05105HX69DB00

Copeland Compressor ZR190KCE-TWD-426

NMB-MAT Fan BM5125-04W-B39