Installation of fittings of air-conditioning water system
Air-conditioning water system includes cooling water system (cooling water pipe, pump, cooling tower, condenser, valve, etc.), chilled water system (chilling water pipe, pump, terminal, valve, insulation, expansion tank, etc.) and condensate water system.
1. Advantages and disadvantages of air conditioning water system
1. Advantages:
①, high temperature control accuracy, constant temperature, no cold and hot phenomenon, good comfort.
②, low operating noise, but also your comfortable and quiet environment.
③. This machine has a low operating cost, even if it is only used in one room, because there is a water temperature control switch, it will stop for a long time and will not waste electrical energy.
2. Disadvantages:
①. High requirements for water system installation and heat preservation must be performed by a professional team to prevent water leakage.
②. The material of the water pipe is high, and it is recommended to use PP-R pipe.
③. The later maintenance is troublesome, there are many auxiliary parts, and the system failure rate is increased. If it is not maintained in time, the heat exchange efficiency will be reduced and the operating cost will be greatly increased.
2. Installation of fittings for air-conditioning water system
1. The design position of the pump in the system
Water flowing in the pipe has frictional resistance (also called along-path resistance or length resistance) and resistance (called local resistance) through various parts (such as elbows, valves, tees, equipment, etc.). The pressure (head) provided by the pump is required Overcome these resistances.
Generally speaking, the chilled water pump should be located at the front end of the chiller, and the chilled water coming back from the end is pumped back to the chiller through the chilled water pump; the cooling water pump is located on the water path of the cooling water entering the unit, and the cooling water from the cooling tower is pumped by the cooling water pump. Return to the unit; the hot water circulating pump is located on the return water main pipe, and the hot water returned from the end is returned to the plate heat exchanger through the hot water circulating pump.
2. Valve design on cooling tower
Cooling tower: A heat exchange device that uses natural ventilation or mechanical ventilation to cool hot water. The cooling tower is a hybrid heat exchanger. The cooling of the cooling water in the tower is mainly due to the evaporation and heat dissipation of water and the contact convection heat exchange between air and water.
①, add a solenoid valve on the cooling tower inlet pipe (manual valve is not recommended).
②, the pipe drain valve should be installed indoors (if it is placed outdoors, because there is some water in the pipe, it is easy to freeze in winter).
3, water quality treatment
①, water filtration: water filter is also called sewage drainer, usually installed in front of measuring instrument or actuator. Need to be cleaned regularly. Regardless of open and closed systems, water filters must be considered in system design. At present, the commonly used water filter devices include metal mesh, Y-type pipe filters, and straight-through decontamination devices. Generally installed on the inlet pipes of chillers, water pumps, heat exchangers, electric control valves and other equipment
②. Closed water system: softened water treatment equipment and corresponding water supplement system must be installed in cold and hot water systems.
Closed system advantages:
A. Since the pipeline is in contact with the atmosphere, the pipeline and equipment should not be corroded.
B. There is no need to provide hydrostatic pressure for high-altitude equipment. The pressure of the circulating water pump is low, so the power of the water pump is relatively small.
C. Since there is no return water tank, gravity return water is not required, and there is no need for return water; additional water pumps are installed, so the investment is low and the system is simple.
Closed system disadvantages:
A. The cold storage capacity is small, and the refrigerator needs to be started frequently when the load is low.
B. The water supply of the expansion tank sometimes requires a pressurized water pump.
③, the installation position of the electronic water treatment instrument: placed behind the water pump, in front of the host.
4. Valves before and after the pump
valve: its function is to connect, cut off and adjust the flow of water or other fluids. Commonly used valve forms in central air conditioning water systems include stop valves, gate valves, butterfly valves, check valves, regulating valves, safety valves, and condensate traps.
①, the water pump inlet pipe is connected in sequence: butterfly valve-pressure gauge-soft connection
②, the outlet pipe of the water pump is connected in sequence: soft connection-pressure gauge-check valve-butterfly valve
5, points, water collector
In central air-conditioning, in order to facilitate the flexible and convenient flow distribution and adjustment of each air-conditioning system zone, water separators and water collectors are often installed on the water supply and return pipes of the water system, and the water supply pipes and return pipes of each air-conditioning zone are connected respectively.
More than two-way supply of air-conditioning water system, it is advisable to install a water collector. The diameter of the collector and manifold should be initially selected according to the cross-sectional velocity (0.5-1.0m/s) when the total flow passes through, and should be greater than 2 times the diameter of the z* large connection opening; the diameter of the cylinder, the manifold and the collector Confirmation of D:
①. Determine the D sub-cylinder according to the cross-sectional flow rate and calculate it according to the cross-sectional flow rate of 8-12m/s;
②, the water separator and the water collector are calculated according to the section velocity of 0.1m/s.
③. Determine D according to the empirical formula, D=(1.5-3) DMAX. DMAX is the maximum diameter of the branch.
④, add an electric differential pressure bypass valve and a bypass pipe between the divider and the water collector (the pipe diameter is generally DN50).
⑤. A thermometer should be installed on the return pipe of the water collector.
6, the location of various meters
Arrange temperature gauges, pressure gauges and other measuring instruments in a place that is convenient for observation. The valve height is generally 1.2-1.5m above the ground. When it is higher than this height, a working platform should be installed.
Pressure gauges: pressure gauges should be installed on the pipes outside the chillers, water inlet and outlet pipes, water pump inlets and outlets, and the branch valves of the water collector and splitter;
Thermometer: Thermometers should be installed in the water inlet and outlet pipes of the chiller and heat exchanger, the water collector and manifold, and the branch valves of the water collector, and the water supply and return branch pipes of the fresh air unit.
7. Discharge and exhaust of water system
①. At the lowest point of the water system, a drain pipe and a drain valve should be installed, and the draining time is 2~3h.
②. At the highest point of the water system, a gas collecting tank should be designed, and a venting device should be installed at each highest point (when there is no slope laying, at the end of the horizontal pipe flow).
8. Selection of differential pressure bypass valve
In the variable water volume water system, in order to ensure a constant flow of chilled water flowing through the evaporator in the chiller, a bypass pipe is installed on the water supply and return mains of multiple chillers. A bypass regulating valve for differential pressure control is installed on the bypass pipe. The maximum design flow is determined by the chilled water volume of a chiller, and the pipe diameter is directly selected according to the maximum allowable flow rate of the chilled water pipe.
9. The location of the unit
The distance between the protruding parts of the two compressors is less than 1.0m, the distance between the refrigerator and the wall and the distance between the non-main passages is not less than 0.8m, and the distance between large and medium-sized refrigeration units (centrifugal, screw, absorption refrigerator) is 1.5~2.0m. The upper part of the refrigeration room of the refrigeration unit should preferably reserve a hook for lifting the largest part or set an electric lifting device.
Installation of fittings of air-conditioning water system
Recent related posts
08/11/2020
Installation of fittings of air-conditioning water system
Air-conditioning water system includes cooling water system (cooling water pipe, pump, cooling tower, condenser, valve, etc.), chilled water system (chilling water pipe, pump, terminal, valve, insulation, expansion tank, etc.) and condensate water system
08/11/2020
Installation conditions and precautions of refrigeration compressors
The selection of the installation site is most ignored by the staff. Often after the compressor is purchased, you can find a location and use it immediately after piping. There is no prior planning at all.
08/11/2020
How to use semi-hermetic refrigeration compressor to save energy
The increasing population has made the problem of scarcity of resources increasingly serious, especially some non-renewable resources, which have become the focus of the struggle between countries.
08/11/2020
How to use central air-conditioning air-cooled water unit
One of the more prominent problems in the central air-conditioning water system is hydraulic imbalance. For some large-scale and more complex systems, there are usually many control loops.
08/11/2020
How to solve various problems such as water leakage, noise, and excessive fluorine leakage of air conditioners
When the air conditioner is in use, there are problems such as water leakage, electric leakage, insufficient cooling and heating, excessive noise, etc., which makes the friends feel particularly heartbroken. Buying an air conditioner to solve this problem and that problem is a headache.
08/11/2020
How to maintain the lubrication system of the chiller
In the operation system of the chiller, more attention is paid to the refrigerant circulation system, the chilled water circulation system and the electrical control system of the refrigerator. The lubrication system is often overlooked. As everyone knows, this system is also very important to the chiller.
08/11/2020
How to effectively reduce the noise of the fresh air system
During the installation and construction of the fresh air system, the fresh air system engineers often encounter that after the fresh air system is installed, the wind speed in the bedroom or study room is too high and the noise is too large
08/11/2020
How to choose a dedicated central air conditioner in a supermarket
Everyone should be familiar with central air-conditioning. It is widely used in our homes and some public places. It can adjust the temperature in the house very well and can bring good ventilation effects.
08/11/2020
How to check the air tightness of refrigeration equipment correctly
The refrigeration equipment is kept under a proper vacuum for a certain period of time. Whether the reading of the vacuum pressure gauge changes to reflect and observe whether the air penetrates into the system to check the sealing performance of the system.
08/11/2020
How to budget for central air conditioning configuration
The standard central air-conditioning budget is roughly composed of three parts: a configuration table, a specific quotation and a detailed list of auxiliary materials.
Customers frequently viewed

IWAYA DENKI Water Pump 25CJT0752
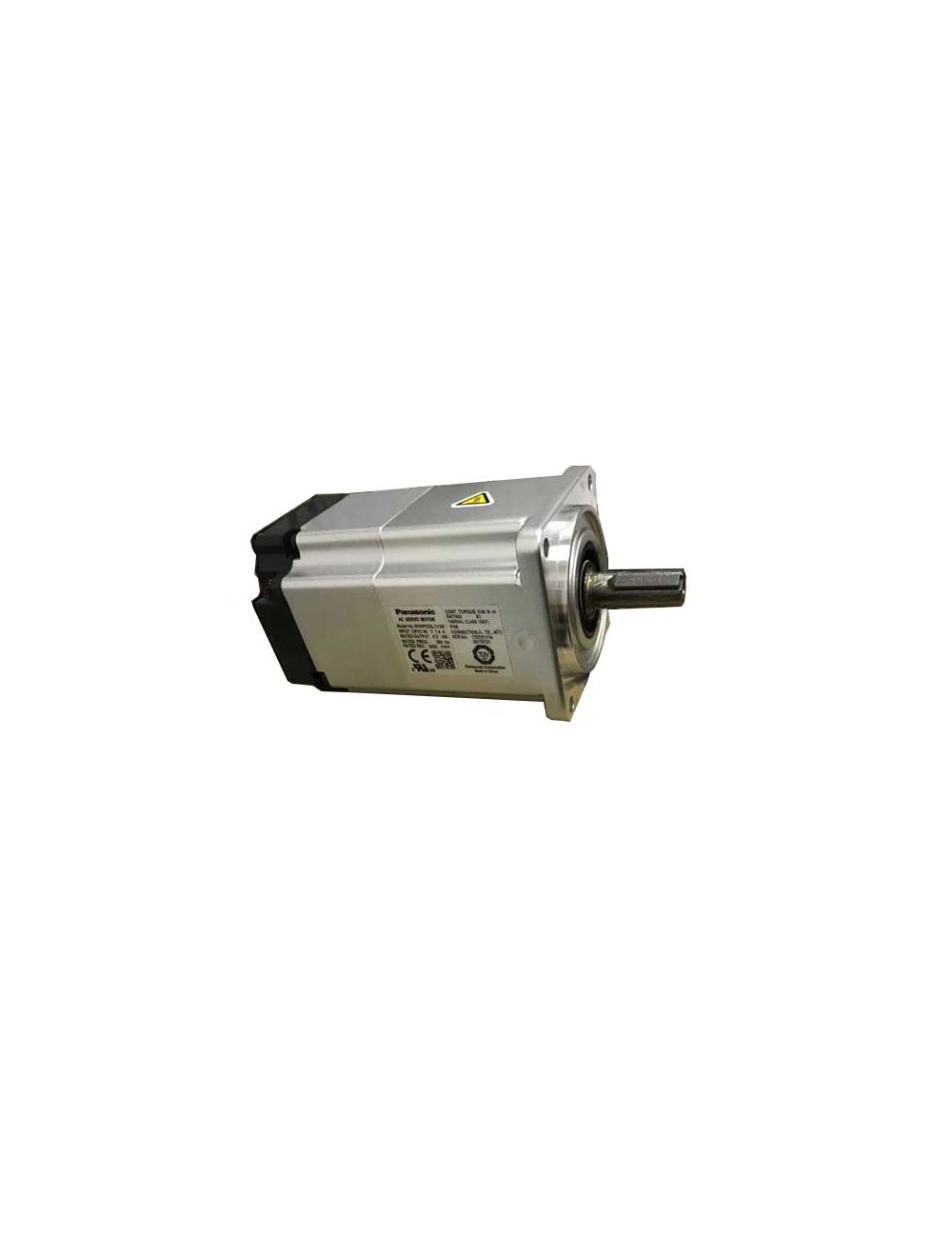
Panasonic Servo Motor MHMF022L1V2M

Honeywell Solenoid Valve VE4025B1045

ROTEN Mechanical Seal 8E5K-22-X

Convo VFD FSCZ02.1-90K0-3P380-A-DP

CKD Solenoid Valve AB21-01-3-000B

AirTAC Air Cylinder SEJ63X100-50S
HONGFA Relay HF7520-048-Z

BANDO Belt T2.5-160-6