Screw compressor working principle and structure analysis
The screw-type refrigeration compressor has a simple structure and a small number of parts. There are no wearing parts such as air valves and piston rings. Its main friction parts such as rotors and bearings have high strength and wear resistance, and good lubrication conditions. Therefore, the amount of machining is low, the material consumption is low, the operation cycle is long, the use is relatively reliable, the maintenance is simple, and it is beneficial to realize the automation of operation.
Compared with the speed compressor, the screw compressor has the characteristics of forced air delivery, that is, the discharge volume is almost not affected by the discharge pressure, and the surge phenomenon does not occur at a small discharge volume. Within, it can still maintain a high efficiency.
Adopts slide valve adjustment, which can realize energy stepless adjustment. There is no clearance volume, so volumetric efficiency is high.
Screw compressors are not sensitive to liquid inlet and can be cooled by oil injection. Therefore, at the same pressure ratio, the discharge temperature is much lower than that of the piston type, so the single-stage pressure ratio is high.
2. Working principle of screw compressor
Inhalation process
When the rotor rotates, the cogging volume gradually expands as the rotor rotates, and communicates with the suction port. The gas from the evaporation system enters the cogging volume through the orifice for the gas suction process. After the rotor rotates to a certain angle, the volume between the teeth crosses the position of the suction orifice and is disconnected from the suction orifice, and the suction process ends.
Compression process
When the rotor continues to rotate, the gas in the tooth groove closed by the body, the suction end seat and the exhaust end seat is pressed toward the exhaust end due to the mutual engagement of the female and male rotors and the mutual filling of the teeth, and the pressure Gradually increase the compression process.
Exhaust process
When the rotor rotates so that the cogging space communicates with the exhaust port on the exhaust end seat, the gas is pressed out and discharged from the exhaust flange port to complete the exhaust process. Because the above three processes must occur in the working cycle of each cog slot, when the compressor is running at a high speed, several pairs of cog slots' working volume repeat the suction, compression and exhaust cycles, so that the compressor The gas is continuous and stable.
3. The role of refrigeration oil and oil circuit equipment
Oil separator
The following conditions ensure that the oil is separated from the refrigerant: 1. The flow rate of oil and gas is different; 2. It flows to the oil tank after hitting the wall; 3. It is blocked after passing through the "atomizer assembly".
Oil filter
Shows the cleaning status by the pressure drop, the normal pressure drop <1 bar, if the DP (pressure difference)> 3.5, the filter is dirty and must be replaced.
Oil heater
Oil heater: During the shutdown period, the heater prevents excessive refrigerant from being diluted into the oil. When the compressor is stopped, the heater should be powered on and run at startup.
Oil level
Oil level: It can be observed through the sight glass. Generally, the oil level should be kept between 1/2-3/4 of the sight glass. In any case, the oil level can be observed through the sight glass for a long time or too much. The bubbles indicate that the oil is diluted by the refrigerant.
4. Inhalation filter
Suction filter: used to eliminate impurities in the medium to protect the normal use of valves and equipment. When the fluid enters the filter cartridge with a certain filter screen, its impurities are blocked, and the clean filtrate is discharged from the filter outlet.
5. Check valve
Non-return valve: Stop to prevent high-pressure gas from returning from the condenser to the compressor. Prevent the impact of reverse pressure on the compressor and the reverse rotation of the rotor.
6. System protection device
Exhaust gas temperature monitoring: lack of oil will cause the exhaust gas temperature to rise suddenly, and the electronic protection module can monitor the exhaust gas temperature.
Pressure difference switch HP / LP: uses its on-off capability to control on-off, in order to ensure that the equipment can shut down the protection equipment in time when the pressure is abnormal.
Oil level control: It is recommended to use the oil level monitor to strictly control the oil level in these applications (long piping arrangement, long distance arrangement of the condenser)
7. Cooling capacity control
According to the cooling capacity of 100-75-50-25%, the slider has 4 corresponding positions. The slider is directly connected to the sliding valve moving in the hydraulic cylinder. The position of the sliding valve is controlled by the solenoid valve. The actual shape of the sliding valve Change the suction port.
Recent related posts
06/14/2020
Screw compressor working principle and structure analysis
1. Features of screw compressor The screw-type refrigeration compressor has a simple structure and a small number of parts.
06/14/2020
Refrigeration compressor installation conditions and precautions
The selection of the installation site is ignored by the staff. Often the compressor will be found at random after it is purchased and used immediately after piping.
06/14/2020
Don't panic if the refrigeration compressor suddenly stops, remember these methods!
What should be paid attention to when the refrigeration compressor stops abnormally? Some friends may not understand it. Let's take a look at it with everyone today!
06/14/2020
Do you know question and answer with refrigeration compressors?
1. Why control the impurity content and moisture content of the compressor and air conditioning system?
06/14/2020
About refrigeration compressor overload protector, we must understand these things
1. Why does the compressor produce overheat protection?
06/14/2020
GLOBAL REFRIGERATION COMPRESSOR MARKET ON TOP TRENDING KEY PLAYERS Mitsubishi Compressor Bristol Compressor
Global Refrigeration Compressor Market on top Trending key players Mitsubishi Compressor Bristol Compressor..
06/14/2020
Liquid Refrigerant, Dense Vapors Can Damage Compressors
To prevent these conditions
06/14/2020
Top 3 Applications for a Servo Motor
Servo motors are essentially electric motors with inbuilt motor
06/14/2020
Danfoss cocuses on providing energy efficient, sustainable and smart refrigeration compressors for a varied range of commercial applications such as cold rooms
Customers frequently viewed

IWAYA DENKI Water Pump 25CJT0752
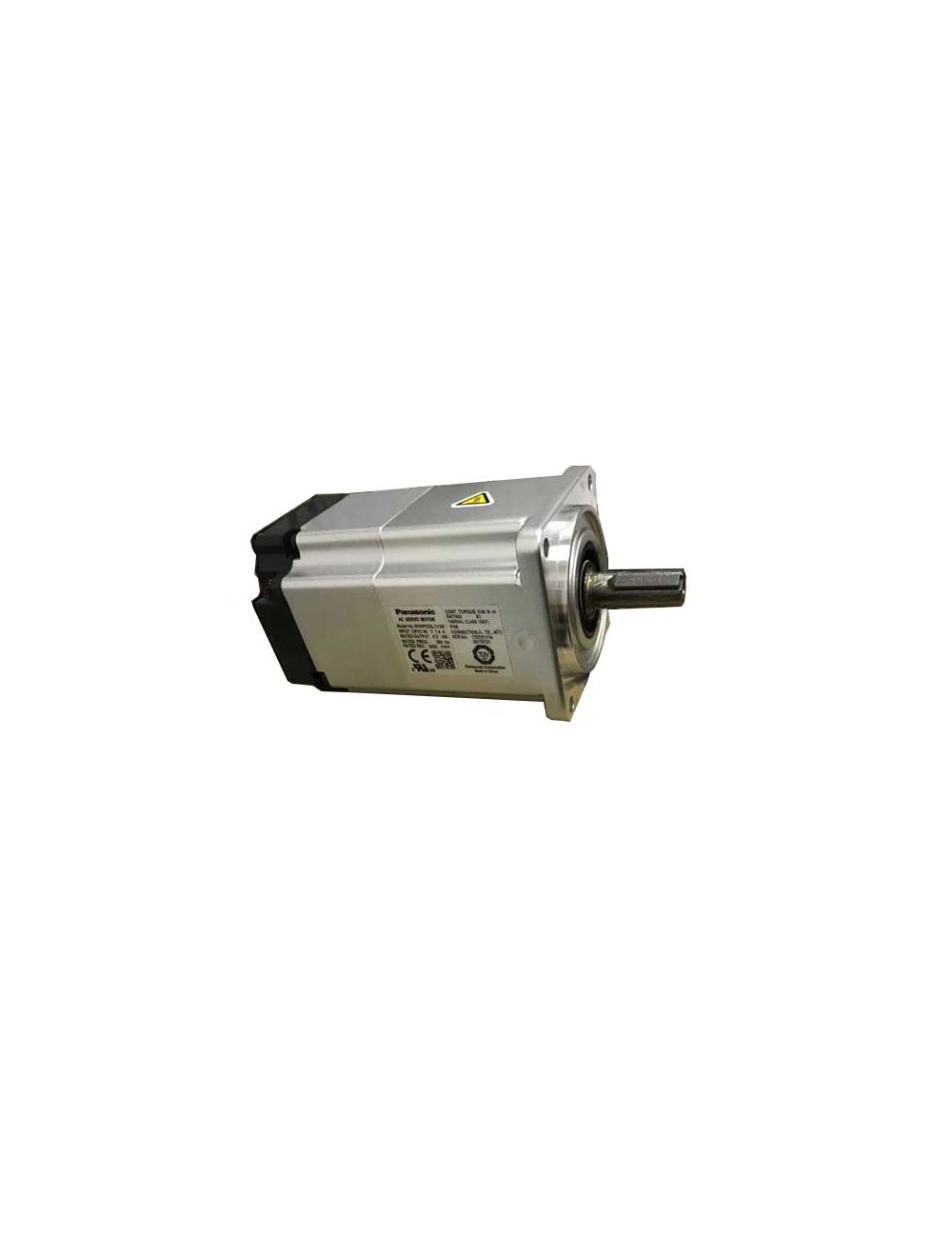
Panasonic Servo Motor MHMF022L1V2M

Honeywell Solenoid Valve VE4025B1045

ROTEN Mechanical Seal 8E5K-22-X

Sanyo Denki Fan 9A0924M4D01

AirTAC Air Cylinder SC40X560