The reason why the compressor of industrial chiller cannot start
What is the reason why the industrial chiller cannot be started? The compressor is the core part of the industrial chiller. If it cannot be started, the entire unit cannot operate normally. When the compressor is started, you should learn more about the data range of various instruments and meters during the normal operation of the industrial chiller refrigeration system, so that you can eliminate various industrial chiller operating faults based on the relevant data.
Industrial chiller cannot be started, it can be ruled out according to the following experience
1. Check the main circuit first. For example, whether the power supply has electricity, whether the voltage is normal, whether the fuse has been blown due to starting overload, whether the air switch is tripped, whether the switch contacts are good, and whether the power supply lacks phase. Observe the voltmeter and ammeter when starting. When the chiller is not equipped with an ammeter or voltmeter, use a multimeter or a tester to check the power supply. When the power supply voltage is too low, the compressor cannot be started.
2. For piston refrigeration compressors, whether the large-end bearing bushes and the curved sleeves of the connecting rods hold shafts. These can be caused by the excessively high exhaust temperature during the previous operation, or it can be caused by the coking of the lubricating oil, which makes the cylinder and the piston stick together, which prevents the compressor from starting.
3. Check the differential pressure relay and high and low voltage relay. When the oil pressure of the compressor is abnormal, the compressor can be stopped. At the same time, when the compressor discharge pressure and suction pressure are abnormal, neither can start or the compressor will stop running soon after it has started.
4. Check whether the amount of chilled water, cooling water, and water temperature are normal. If the water volume is small and the water temperature is high, the condensing pressure will rise sharply, and the evaporation temperature will drop rapidly. Due to the action of the unit protection facilities, the unit will often shut down quickly.
5. Check whether the relevant solenoid valve and regulating valve are out of order, and whether they are opened or closed as required.
6. Check whether there is a leakage of working fluid in the temperature sensing bag of the temperature relay, or the adjustment is wrong.
The following work should be done before starting the industrial chiller
1. First check whether the power supply is normal. The power supply voltage should not exceed or be lower than ±10% of the rated voltage of the unit. Commonly used voltages are 3-phase 380V and single-phase 220V. When the voltage is too low or too high, the chiller cannot be started.
2. For compressor units with a water system, carefully check whether there is water in the cooling water system and the chilled water system, whether the water pressure is normal, and whether the cooling water and chilled water pipeline systems are unblocked.
3. Check whether various pressure gauges, thermometers, flow meters, solenoid valves, relays, and energy regulating valves of industrial chillers are in good condition.
4. Check the transmission device, if it is driven by a belt, whether its various protective devices are completely reliable, and whether all kinds of wrong equipment and protective equipment are complete and effective.
5. Check whether various valves of the high-pressure system and low-pressure system of the industrial chiller are in the correct switching state when starting or running.
6. Check the crankcase lubricant. The oil level should not be lower than or higher than the indicated oil level. If the lubricating oil is not enough, add enough lubricating oil of the same specification and model.
7. Check whether the refrigerant system of the industrial chiller is leaking, and whether the lubricating oil system is leaking.
8. Check whether the liquid level of the liquid storage tank is normal, and the liquid level should be kept between one-third and two-thirds.
9. Read shift records, installation and repair records, reports and drawings.
The role of industrial chillers is to provide industrial chilled water to cool the equipment to ensure the stability of product quality and improve the production efficiency of the entire factory. During use, carefully observe and listen to the sounds and abnormalities of the various components of the unit, and regularly maintain the chiller. When the unit is not used for a long time, drain the water from the pipeline and cover the unit with objects, etc. .
The reason why the compressor of industrial chiller cannot start
Recent related posts
08/20/2020
The reason why the compressor of industrial chiller cannot start
What is the reason why the industrial chiller cannot be started? The compressor is the core part of the industrial chiller. If it cannot be started, the entire unit cannot operate normally. When the compressor is started,
08/20/2020
The principle and decisive factors of cooling tower cooling effect
The role of the cooling tower is to exchange the cooling water carrying waste heat with the air inside the tower body, so that the waste heat is transferred to the air and dispersed into the atmosphere.
08/20/2020
The main difference between air-cooled chillers and water-cooled chillers
First of all, it is necessary to find out which types of chillers are divided into: General manufacturers will produce two types of water-cooled and air-cooled chillers.
08/20/2020
The installation and use of air-conditioning are particular about these skills
The air conditioner is our favorite when it's hot, and when it's hottest, the air conditioner often turns on the shaft and can't stop for a moment. Some friends even bought an air conditioner and installed it when the weather was too hot.
08/20/2020
The general layout principle of the suction pipe in the cold storage
Recently, a small partner left a message asking about the general layout principles of the suction pipe in the cold storage. Today, the editor of okmarts.com will popularize this knowledge for everyone
08/20/2020
The difference between cross-flow cooling tower and counter-flow cooling tower
The so-called cross-flow cooling tower is a type of cooling tower that allows air to flow horizontally through the water spray filler, and the water dragon falls vertically from the top of the tower
08/20/2020
The difference and advantages and disadvantages of air duct machine, water chiller and multi-line
1. Ducting machine-Ducting system duct type system, as its name implies, uses air as the conveying medium. It uses chillers to centrally produce cold energy, cools/heats the fresh air, mixes it with the return air, and sends it indoors.
08/20/2020
The bigger the number of horses, the better Don't get into the misunderstanding when buying air conditioners
Summer is a good time to buy air conditioners, and major air conditioner manufacturers have one after another promotion. So what should consumers pay attention to when buying air conditioners?
08/20/2020
The air conditioner doesn’t cool right after I bought it. I bought a fake brand.
Summer is here, and the sales season for air conditioners is also coming. However, recently some citizens have bought "fake air conditioners." Obviously it is a new product of the well-known brand Midea, why does it stop cooling after just a few days of purchase?
08/20/2020
Technical points of air energy heat pump compressor
In the actual system design, the rules of heat pump operation must also be followed, so that the function of the heat pump special compressor can be truly utilized. Specifically, the following aspects should be noted:
Customers frequently viewed

IWAYA DENKI Water Pump 25CJT0752
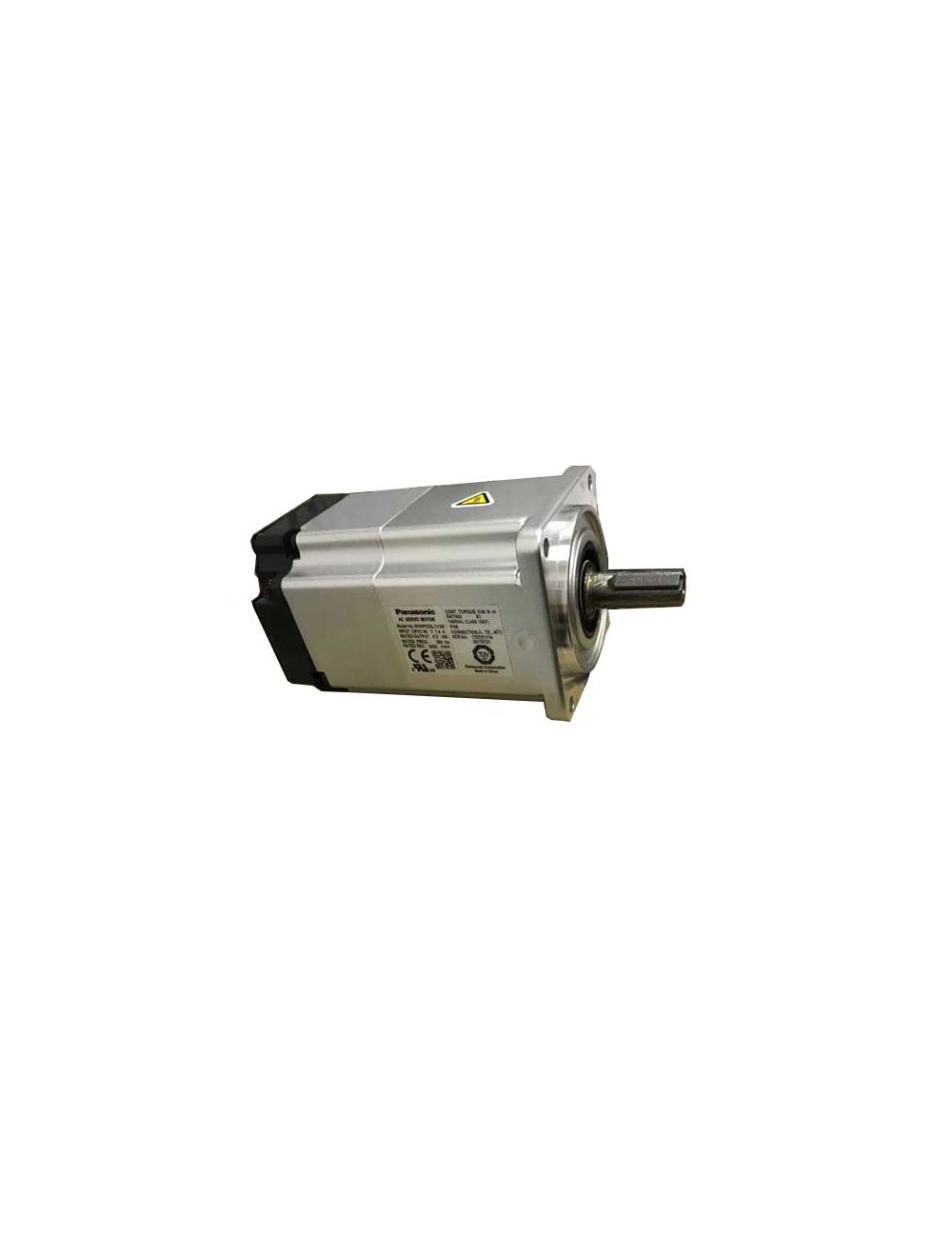
Panasonic Servo Motor MHMF022L1V2M

Honeywell Solenoid Valve VE4025B1045

ROTEN Mechanical Seal 8E5K-22-X

ADDA Fan AG04012UB157100

AirTac Solenoid Valve 5V420-15F200

Siemens Contactor 3RT2017-4AN62

SCHNEEBERGER Linear Guideway BMA15-G3V1