Compressor installation
Compressor installation
Chapter 1 General Provisions
Article 1 This chapter is applicable to the installation of reciprocating piston type, screw type, vane type and membrane type positive displacement compressors.
Article 2 This article is the professional technical regulations for compressor installation engineering. The general technical requirements for installation engineering shall be implemented in accordance with the provisions of the "General Regulations" in the first volume of this code.
The disassembly and cleaning of the compressor should meet the following requirements;
1. The compressor installed as a whole should generally be disassembled and washed as follows;
1. For reciprocating piston compressors, the piston, connecting rod, air valve and packing should be removed, and the equipment surface and the removed parts and components
Clean the valve and packing without steam;
2. When the reciprocating piston compressor sealed with oil seal lubricating oil is installed within the oil seal period specified in the equipment technical document,
Except for the air valve, other parts and components are not removable and washable.
3. Screw compressor and sliding vane compressor are installed within the oil seal period specified in the equipment technical documents. Can not be disassembled
Washing, if there are special requirements, follow the equipment technical documents;
4. Membrane compressors should be dismantled and washed the rainbow cover, diaphragm and suction and exhaust valves.
2. Compressors assembled on site should be cleaned of the main engine parts, components and auxiliary equipment. Valves, packings and other seals should not be steamed
Steam cleaning, after cleaning, the cleaning agent or water should be removed, and the parts, equipment and equipment surface should be inspected for defects such as damage.
Apply a thin layer of lubricating oil (zero parts of non-lubricated compressors that come into contact with the medium, and parts are not coated with oil).
Chapter 2 Integrated compressor
Article 4 The vertical and horizontal non-levelness of the compressor should not exceed 0.2/1000. It should be measured at the following locations:
1. Horizontal compressors (including symmetrical balance type) are measured on the slide surface of the fuselage or other reference surfaces;
2. Remove the cylinder head of the vertical compressor and measure on the plane of the cylinder top;
Other types of compressors are measured on the exposed part of the main shaft or other reference surfaces.
Chapter 3 Reciprocating Piston Compressors Assembled on Site
Article 5 The assembly of the fuselage and the middle body shall meet the following requirements:
1. Use kerosene to inject into the fuselage to the highest oil level of the lubricating oil, and there shall be no leakage after 8 hours;
2. The vertical and horizontal levels of the fuselage should not exceed 0.05/1000. And should be measured at the following locations;
1. The horizontal unevenness of the horizontal compressor (including the symmetrical balance type) is measured at the two points of the front and back of the slide, horizontal
Non-levelness is measured at the bearing hole of the fuselage (see Figure V-1.1);
2. The vertical compressor is measured on the joint surface of the fuselage.
3. The L-type compressor is measured on the flange surface of the fuselage.
Third, the different axial degrees of the main bearing hole axis line of the two-body compressor should not exceed 0.05 mm.
Article 6 The assembly of crankshafts and bearings shall meet the following requirements:
1. The oil passages of the crankshaft and bearings should be unobstructed and clean. The oil plug of the crankshaft and the locking device of the balance iron must be tightened;
Second, the bearing steel shell and the bearing alloy layer should be firmly bonded, and there should be no shelling and mute;
3. The back of the bearing pad and the bearing pad should be closely attached, and the contact area should be less than 70%;
Fourth, the radial and axial clearance between the bearing bush and the main journal should comply with the provisions of the technical documentation of the equipment;
Fifth, the contact arc surface of the bottom tile of the split thick-walled bush and the journal should not be less than 900, and its contact area should not be less than the contact arc surface
70% of ; four-way bearing, the contact area of the journal with the lower and side tiles should not be less than 70% of the area of each tile; when the thin-walled bearing is assembled
No scraping is required, but the gap should meet the requirements of the technical documentation of the equipment;
6. The level of the crankshaft should not exceed 0.1/1000. At a position of 900 crankshaft revolutions, use a spirit level to measure on the spindle neck;
Seven. The non-vertical degree of the crankshaft axis line to the slideway axis line should not exceed 01/1000 (see Figure V-1.2);
8. Check the distance between the upper, lower, left, and right positions of the crank (see Figure V-1.3). The change value should meet the requirements of the technical documentation of the equipment. If there is no provision, it should not be greater than one ten thousandth of the stroke value.
Nine. After the crankshaft is assembled, it should be turned several times without blocking.
Article 7 The assembled cylinder shall meet the following requirements:
1. After the cylinder is assembled, the waterway should be tested for tightness according to the equipment technical documents, and there should be no leakage;
Second, the different axis degrees of the horizontal cylinder axis to the slide axis should meet the requirements of Table V-1.1, and the direction of its inclination should be the same as that of the slide
The direction of inclination is the same; when adjusting the cylinder core, no gasket should be placed on the end face of the cylinder.
3. When aligning the vertical cylinder, the gap between the piston and the cylinder should be uniform, and the deviation should be less than the average distance between the piston and the cylinder
1/2 of the gap value.
Different axial degrees of cylinder axis to slide axis
Cylinder diameter (Bomm)
Radial displacement should not exceed (mm)
Tilt should not exceed
≤100
0.05
>100~300
0.07
0.02/1000
>300~500
0.10
0.04/1000
>500~1000
0.15
0.06/1000
>1000
0.20
0.08/1000
Article 8 The assembly link shall meet the following requirements:
1. The oil path of the connecting rod should be smooth and clean;
2. The contact area between the thick-walled connecting rod big head tile and the crank pin should not be less than 70% of the area of the big-end tile; the thin-walled connecting rod big head tile is not
To be scraped, the contact area of the connecting rod small bush (bearing bush) and the crosshead pin should not be less than 70% of the area of the small bushing (bearing bush).
3. The radial clearance and axial clearance of the connecting rod big head tile and the crank pin shall comply with the provisions of the equipment technical documents;
4. The radial clearance between the connecting rod small bush (bearing bush) and the cross head pin, and the axial clearance between the small head bush (bearing bush) and the cross head body
Should comply with the provisions of equipment technical documents;
Fifth, the connecting rod bolts and nuts should be tightened and locked evenly with reference to the tightening torque recommended by the technical documentation of the equipment.
Article 9 The assembled crosshead shall meet the following requirements:
1. The contact area between the cross-head shoe and the slideway should not be less than 60% of the shoe area;
Second, the gap between the crosshead shoe and the slideway should meet the requirements of the technical documentation of the equipment at each position of the stroke;
3. Symmetrical balanced compressors, the crossheads on both sides of the fuselage make symmetrical movements, and the force direction of the shoes is different.
The mark made by the manufacturer shall be carried out to prevent wrong installation to ensure that the axis of the piston rod coincides with the axis of the slideway;
4. The connecting bolts and locking devices of the crosshead pins should be tightened and tight.
Article 10 The assembled piston and piston rod shall meet the following requirements
1. The piston ring should be inspected for light leakage in the cylinder first. There should be no more than two light leakages on the entire circumference, and each should not exceed a 45 degree arc
Long, and the distance from the opening of the piston ring should be greater than 30 degrees (except for the plastic ring);
Second, the gap between the piston ring and the end surface of the piston ring groove, and the opening gap of the piston ring into the cylinder should conform to the technical documents of the equipment
regulations;
3. The piston ring should be able to rotate freely by hand in the piston ring. When the piston ring is pressed by hand, the ring should be able to sink completely into the groove, and the piston is filled with gas
In the cylinder, the opening positions of the same group of piston rings should be staggered from each other, and all the opening positions should be staggered from the valve hole;
Fourth, the gap between the piston and the mirror surface of the cylinder should meet the requirements of the technical documentation of the equipment. For the horizontal cylinder and the bottom with bearing alloy
The upper clearance of the piston is allowed to be less than about 5% of the average clearance than the lower clearance;
Fifth, the contact area of the piston bearing surface cast with the piston bearing alloy and the cylinder mirror surface should not be less than 60% of the piston support arc surface.
VI. Piston rod and piston, piston rod and cross head should be firmly connected and locked;
7. The clearance between the piston's inner and outer dead center of the cylinder shall comply with the provisions of the technical documentation of the equipment.
Article 11 The assembly filling and oil scraper shall meet the following requirements:
1. When assembling the packing, its oil, water and air channels must be unobstructed and clean;
2. The contact area of each packing ring end face and packing box end face should not be less than 70%;
3. The contact area between the filler, the oil scraper and the piston rod should not be less than 70% of the ring area of the group;
4. When the oil scraper is assembled, the oil scraping blade should not be rounded, and the direction of the blade should not be reversed;
Five, after the packing and the oil scraper are assembled, the gaps everywhere should conform to the equipment technical documents;
6. The locking device of the packing gland must be locked.
Article 12 The assembled gas valve shall meet the following requirements:
1. The spring force of the air valve spring should be uniform, and the valve plate and spring should not be stuck or skewed;
Second, the air valve adjustment device and valve lift should comply with the equipment technical documents.
3. After the valve is assembled, kerosene should be injected for the tightness test. Only discontinuous drop leakage is allowed.
Article 13 The assembled lubrication system shall meet the following requirements:
1. There should be no sharp bends, twisting and flattening in the tubing;
2. The transmission mechanism connecting the crankshaft and the oil pump or the crankshaft and the oil injector should operate flexibly;
3. The pipelines, valves, filters and coolers of the lubricating system, etc., after assembly, should be strictly controlled according to the pressure specified in the technical documentation of the equipment.
If there is no provision for the tightness test, the test shall be carried out according to the rated pressure, and there shall be no leakage.
Fourth, the oil pipe should be discharged through the exhaust first, and then connected to the oil supply lubrication point.
Chapter 4 Ancillary equipment
Article 14 Before the accessory equipment of the compressor (such as cooler, gas-liquid separator, buffer, dryer, gas storage tank, filter, emptying tank, etc.) is in place, the orientation and ground Whether the positions of the foot bolt holes and the foundation match, and check whether the pipelines are smooth.
Article 15 The ancillary equipment under pressure shall be tested for strength and tightness according to the pressure specified in the technical documents. If not specified, the strength test pressure shall be carried out according to the provisions of Table V-12. The tightness test pressure shall be carried out according to the rated pressure.
Auxiliary equipment strength test pressure table V-1.2
Tilt pressure P (kgf/cm)
Test pressure PS (kg/cm2)
12
1.5P
P+3
1.25P
Article 16 The strength test shall use water as the medium, and the equipment shall be maintained under the test pressure for 5 minutes, and then the pressure shall be reduced to the rated pressure, and a small hammer shall be tapped along the 150 mm sides of the weld for a comprehensive inspection. There shall be no leakage or Deformation and other phenomena.
Article 17 When using air or inert gas as the medium for the tightness test, the following methods should be used for inspection:
1. Use soapy water to coat the joints of bolts, riveting and welding, and observe whether there are bubbles;
2. The leakage or pressure drop of the gas within every hour (at least 1 hour of observation) should meet the requirements of the equipment technical documents.
Article 18 When the auxiliary equipment under pressure meets the following three conditions at the same time, the strength test may not be conducted, but only the tightness test;
1. The strength test has been done at the manufacturer and has a certificate of conformity;
2. The appearance is not damaged;
3. Install within the specified time limit of the technical documents.
Article 19 The non-levelness of the discharge pipe of the water-cooled cooler and the non-vertical degree of the vertical surface of the discharge pipe shall comply with the provisions of the technical documentation of the equipment; when there is no provision, they shall not exceed 1/1000; Evenly.
Article 20 The horizontality of the horizontal equipment and the verticality of the vertical equipment shall meet the requirements of the technical documents of the equipment; when there is no regulation, they shall not exceed 1/1000.
Chapter 5 Commissioning
Article 21 The compressor shall meet the following requirements before trial operation
1. Fasteners such as cylinder head, cylinder, airframe, cross head, connecting rod, bearing cap, etc., should be fully reviewed for tightness;
Second, the instrument and electrical equipment should be adjusted correctly, and the direction of the motor should meet the requirements of the compressor;
3. The quantity and quantity of lubricating grease should be in accordance with the equipment technical documents, and the oil supply should be normal;
Fourth, the intake pipe should be clean;
Fifth, the water inlet and drain pipes should be unblocked;
6. Turn the compressor several times, it should be flexible without blocking phenomenon;
7. Safety valves at all levels should be sensitive.
Article 22 The compressor shall meet the following requirements during the no-load trial operation;
1. Remove the suction and exhaust valves at all levels;
Second, start the compressor and stop running immediately, check each part, after no abnormality, then run for 5 minutes, 30 minutes and
4~8 hours, before each operation, you should check whether the lubrication of the compressor is normal;
3. The oil pressure, high temperature and temperature rise of each friction part during operation shall comply with the provisions of the equipment technical documents;
Fourth, all moving parts during operation should be free of abnormal noise, and each fastener should not be loose.
Article 23 The compressor air load test run shall meet the following requirements;
First, before the air load trial operation, the air filter should be installed first, and the suction and exhaust valves should be installed step by step to start the compressor to blow
Wash. Starting from the first level, connect the purging step by step until the exhaust air is clean, but the purging time of each level should not be less than 30 minutes,
The purging pressure at all levels should be in accordance with the technical documents of the equipment; when there is no regulation, it should be carried out at 1.5 to 2 kgf/cm2
2. After blowing, all levels of suction and exhaust valves should be removed and cleaned, and inspected for damage;
3. Gradually step-up operation, it should be operated for 1 hour at the exhaust pressure of 1/4 of the rated pressure; it should be operated at 1/2 of the rated pressure
2 hours; 3/4 of the rated pressure should be operated for 2 hours; the operating time at the rated pressure should be in accordance with the technical documents of the equipment; no rules
Timing should not be less than 24 hours;
4. During the compressor and booster operation, there should be no abnormal phenomena before the pressure can be gradually increased until it is stable at the required pressure
operation;
Fifth, the compressor whose compression medium is not air, when using air for load test operation, the maximum discharge pressure should be consistent with the equipment technology
The provisions of the document, when not specified, shall not exceed 250 kgf/cm2;
VI. The oil pressure during the operation of the compressor must not be less than 1 kgf/cm2. The temperature of the lubricating oil in the crankcase or the fuselage, with a crosshead
The compressor should not be higher than 60℃, and the compressor without cross head should not be higher than 70℃;
7. The discharge temperature of compressor at all levels should not be higher than 40℃;
8. The vibration and sound of the compressor should be normal.
Article 24 During the air load test run of the compressor, the following inspections and records shall be carried out:
1. The pressure and temperature of lubricating oil and the supply of oil in various parts;
2. Suction and exhaust temperature and pressure at all levels;
3. The inlet and outlet temperature and cooling water supply at all levels
Fourth, the work of suction and exhaust valves at all levels is normal;
Fifth, whether there are abnormal sounds of various moving parts;
Sixth, whether there is air leakage, oil leakage or water leakage in each connecting part;
Seventh, whether there is any looseness in the connection parts;
8. Whether the volume adjustment device is sensitive;
Nine, the temperature of the main friction parts such as the main bearing, slideway, filler, etc.;
Ten. The current, voltage and temperature rise of the motor;
Eleven, whether the automatic control device is sensitive.
Article 25 After the compressor has passed the trial operation, the lubricant should be replaced. Chapter 6 Lubricating Compressors
Article 26 The installation requirements for non-lubricated compressors and their ancillary equipment shall comply with the following requirements in addition to the provisions in Chapters 1, 2, 3 and 4 of this Part:
1. The oil seal parts should be degreased and cleaned before assembly, and there should be no rust on the mirror surface of the cylinder and the surface of the piston rod;
2. After assembling the cylinder and packing, the waterway part should be tested for tightness with water according to the pressure specified in the technical documentation of the equipment.
There should be leakage;
3. The gaps of the packing components shall comply with the provisions of the technical documents of the equipment.
4. The gap between the supporting ring and the mirror surface of the cylinder, the gap between the supporting ring and the end surface of the ring groove, should comply with the specifications of the technical documentation of the equipment
fixed;
Fifth, the assembly of the oil scraper should be in the correct direction of the cutting edge, and it must not be reversed. The oil retaining ring on the piston rod should be firmly assembled;
Sixth, before assembling the piston, there should be a layer of No. 0 molybdenum disulfide powder on the surface of the piston rod and the cylinder mirror surface, and the excess disulfide on the surface
Molybdenum powder is blown clean, if there are special requirements, it shall be carried out according to the provisions of complete technical documents;
7. Internally cooled piston rods, the coolant inlet and outlet pipes should be unblocked, and the pipe joints should be firmly assembled.
Article 27 Compressors whose compressive medium is oxygen and other flammable gases, all parts and components (including piston rods, packings, oil retaining rings), auxiliary equipment and pipelines in contact with the medium, except for oil cleaning, It must also be degreased in accordance with the provisions of Article 50 and Appendix VIII of the “General Provisions" of the first volume of this specification. After degreasing, dry it with oil-free dry air or nitrogen, and seal both ends of the pipeline without oil.
Article 28 The trial operation of non-lubricated compressors shall be carried out in accordance with the procedures and media specified in the technical documents of the equipment. If there are no provisions, in addition to the trial operation of no-load and air-load according to the provisions of Chapter 5 of this PART, the following shall be complied with: Claim;
1. The coolant must be fully supplied during operation. The surface temperature of the piston rod, the exhaust temperature at all levels, and the discharge temperature should meet the requirements of the technical documentation of the equipment;
2. The oil scraping condition on the surface of the piston rod during operation should be good; the lubricating oil of the crankcase and crosshead must not be brought into the cylinder of the packing;
3. During the step-by-step pressure increase process, the pressure should be increased step by step after the temperature reaches a stable state, the packing is well sealed, and no signs of seizure are found.
Article 29 During the completion of construction or suspension of trial operation, anti-rust treatment shall be done; generally, oil-free dry nitrogen shall be introduced into the suction pipe, and the compressor shall be slowly rotated and discharged through the vent valve to make the nitrogen blow out the moisture in the cylinder , And then close the suction and exhaust pipe valves to prevent rust.
Chapter VII Screw compressors assembled on site
Article 30 The following work should be done before assembly:
1. The compressor main unit and auxiliary equipment should be cleaned, and the cleaning agent or water should be removed, and the rotor, bearings, teeth should be carefully checked
Whether the wheels and cylinders are damaged or not, prevent impurities from entering the working chamber, and the cleaning and degreasing of the atmospheric screw compressor should comply with the sixth of this chapter
Article 27 of Chapter ;
Second, the cylinder and rotor of the compressor should be tested for tightness according to the pressure specified in the technical documentation of the equipment.
Article 31 The assembly of cylinders, rotors and gears shall meet the following requirements:
1. The vertical and horizontal microwave non-levelness of the cylinder should not exceed 0.05/1000, and the inclination should be in the same direction, which can be in the cylinder
Measurement on the sub-surface or in the bearing hole;
2. When locating the unit, the axis of the motor shaft (or speed-increasing gearbox shaft) should be taken as the reference, and the different shaft degrees should not exceed the technical specifications of the equipment.
The provisions of the article, when there is no provision, the radial displacement of different axial degrees should not exceed 0.05 mm;
3. Radial clearance between shaft seal and shaft opera, radial clearance between radial bearing and rotor journal, between thrust bearing and thrust disc
The axial clearance shall comply with the provisions of the equipment technical documents;
4. The meshing gap between the screw, the gap between the outer circle of the screw and the cylinder wall, and the gap between the two end surfaces of the screw and the side wall of the cylinder are all
Should comply with the provisions of equipment technical documents;
Fifth, after the cylinder and rotor are leveled, the anchor bolts should be tightened symmetrically and evenly; and placed on the split surface of the cylinder and the rotor journal
Set a spirit level to check the non-levelness of the cylinder and rotor;
VI. The meshing clearance of the gear should conform to the provisions of the equipment technical documents.
Article 32 In addition to the installation of ancillary equipment, in addition to complying with the provisions of Chapter 4 of this Part, the suction and exhaust units shall be flushed with compressed air, and the installation position shall be as close as possible to the suction and exhaust ports of the cylinder.
Article 33 The screw compressor shall meet the following requirements before trial operation:
1. The lubricating system should be cleaned according to the provisions of the equipment technical documents;
2. The cooling water should be supplied normally without leakage;
3. Oil pressure, temperature, cross section, electric bypass valve, overcurrent, undervoltage and other safety interlocking devices shall be in accordance with the technical documents of the equipment
Provisions for inspection and commissioning are passed;
4. At the suction port of the compressor, an air filter in accordance with the technical specifications of the equipment shall be installed;
Fifth, the valve should be fully opened or removed in accordance with the provisions of the technical documentation of the equipment.
Article 34 No-load test operation shall meet the following requirements:
1. The oil pump should be started and operated for not less than 15 minutes under the pressure specified in the technical documentation of the equipment;
2. The motor should be started separately to check whether the rotation direction is correct, and the continuous operation should be no less than 1 hour. Its vibration and bearing temperature
should be normal;
3. After the motor is connected to the compressor, it can be turned several times, and it should be flexible without blocking;
Fourth, the compressor should be started for 2 to 3 minutes, after confirming that there is no abnormal phenomenon, the continuous operation is not less than 30 minutes, and the compressor is stopped for 15 minutes
After , the oil pump must stop running, and then clean the filter of each oil injection port;
Fifth, the compressor should be started again, continuous operation should be carried out for no less than 2 hours for purging, and check whether the temperature of each bearing is normal.
Article 35 The air load test operation shall meet the following requirements:
1. The muffler should be installed at the suction port, and various measuring instruments should be installed according to the provisions of the equipment technical documents.
Close the valve;
2. The compressor should be started for no-load operation for not less than 30 minutes;
3. The bypass valve should be closed slowly, and the pressure should be increased and operated step by step according to the pressure increase rate and operation time specified in the equipment technical documents.
The increase of force makes the compressor warm up slowly;
Fourth, it should be boosted to rated pressure for continuous operation for not less than 4 hours. During compressor and step-up operation, bearing temperature and vibration
After the situation is normal, the pressure must be increased step by step;
V. During continuous operation at rated pressure, the following items should be checked and recorded every half an hour;
1. Lubricant pressure, temperature and oil supply of each part;
2. Suction and exhaust temperature and pressure at all levels;
3. The temperature of each bearing;
4. Inlet and discharge temperatures and cooling water supply at all levels;
5. The current, voltage and temperature rise of the motor.
Article 36 The heating test operation shall meet the following requirements:
1. After the air load test operation is qualified, the temperature increase test should be carried out according to the temperature specified by the equipment technology, and the operation at this temperature should be checked.
reliability;
2. The high-temperature temperature relay should be based on the heating value specified in the equipment technical document;
3. The heating method can be achieved by increasing the exhaust pressure (the pressure relay needs to be adjusted accordingly), or heating the gas at the gas inlet
Required temperature;
Fourth, it should be continuously operated for not less than 2 hours at the specified temperature, and frequently check the bearing temperature, motor current and vibration;
Fifth, after the temperature increase test, the cylinder head should be removed and the rotor should be carefully inspected for traces such as contact damage; at the same time, the temperature should be restored
Degree, the original position of the trigger point of the pressure relay.
Article 37 After the compressor heating test is passed, the sensitivity of the safety valve and differential pressure relay shall be tested according to the pressure specified in the equipment technical document, and its action shall be correct and sensitive.
Article 38 After the compressor has passed the trial operation, the lubricant should be replaced.
Compressor installation
Recent related posts
06/27/2020
Compressor installation
Chapter 1 General Provisions Article 1 This chapter is applicable to the installation of reciprocating piston type, screw type, vane type and membrane type positive displacement compressors.
06/27/2020
Common faults and solutions of compressors
A compressor is a machine that compresses gas to increase gas pressure or transport gas, and is widely used. In the mining industry, metallurgy industry, machinery manufacturing, civil engineering, petrochemical industry, refrigeration and gas separation engineering, and defense industry, compressors are one of the indispensable key equipment.
06/26/2020
What is the refrigerator compressor used for
Refrigerators use evaporative cooling or vaporization to absorb heat to achieve the purpose of refrigeration. The throat of the refrigerator is filled with a refrigerant known commercially as Freon, commonly known as refrigerant. A commonly used one is difluorodichloromethane, which is a colorless, odorless and non-toxic gas with a boiling point of 29°C. Freon is pressurized by the compressor when it is in a gas state.
06/26/2020
Analysis of common faults and solutions of air-conditioning compressors
The air conditioning compressor is the heart of the refrigeration system and the power source for the refrigerant to circulate in the system. The basic working principle of the refrigeration system mainly includes the four processes of compression, condensation, throttling and evaporation.
06/26/2020
What brand of refrigerator compressor is the best
Do you know what the most important parts of a refrigerator are? Of course, it is the compressor. The refrigerator can work normally because of it. It can be said that the compressor is the core component of the refrigerator.
06/26/2020
Compressor starting circuit diagram
[Introduction] Compressor startup circuit diagram. Refrigerators, air conditioners and other appliances, the compressor is driven by a single-phase induction motor. When starting, the induction motor must overcome both its own inertia and high-pressure refrigeration
06/26/2020
Maintenance method of refrigerator compressor without stopping
Maintenance method of refrigerator compressor without stopping The focus of non-stop compressor maintenance is on the cooling effect. If the cooling effect is normal without stopping, the fault is in the thermostat. Otherwise, it is because the system lacks fluorine and the temperature falls below the control point, which results in non-stop. When repairing,
06/25/2020
On the operation principle and internal structure of air-conditioning compressor
On the operation principle and internal structure of air-conditioning compressor Regarding air-conditioning compressors, this belongs to the refrigeration system, which is generally used for air-conditioning and refrigerator cold storage, and belongs to the heart of refrigeration equipment. Air-conditioning compressors can be classified according to different principles, usually divided into two types: volume type and speed type. Volumetric air-conditioning compressors are relatively common and one of the most popular compressors.
06/25/2020
Briefly explain the principle, advantages and disadvantages of screw compressors
Briefly explain the principle, advantages and disadvantages of screw compressors The screw compressor has the characteristics of small size, light weight, easy maintenance, etc. It is a model that develops faster in refrigeration compressors. On the one hand, the screw profile and structural design have made great progress. On the other hand, the introduction of special milling machines for screw rotors, especially grinding machines, has improved the machining accuracy and processing efficiency of
06/25/2020
[Experience] Constant temperature and humidity box refrigeration system
[Experience] Constant temperature and humidity box refrigeration system Constant temperature and humidity box refrigeration system: 1 Two single-stage refrigeration system cascade refrigeration cycle; 2 Cascade refrigeration cycle of two-stage compression system;
Customers frequently viewed

IWAYA DENKI Water Pump 25CJT0752
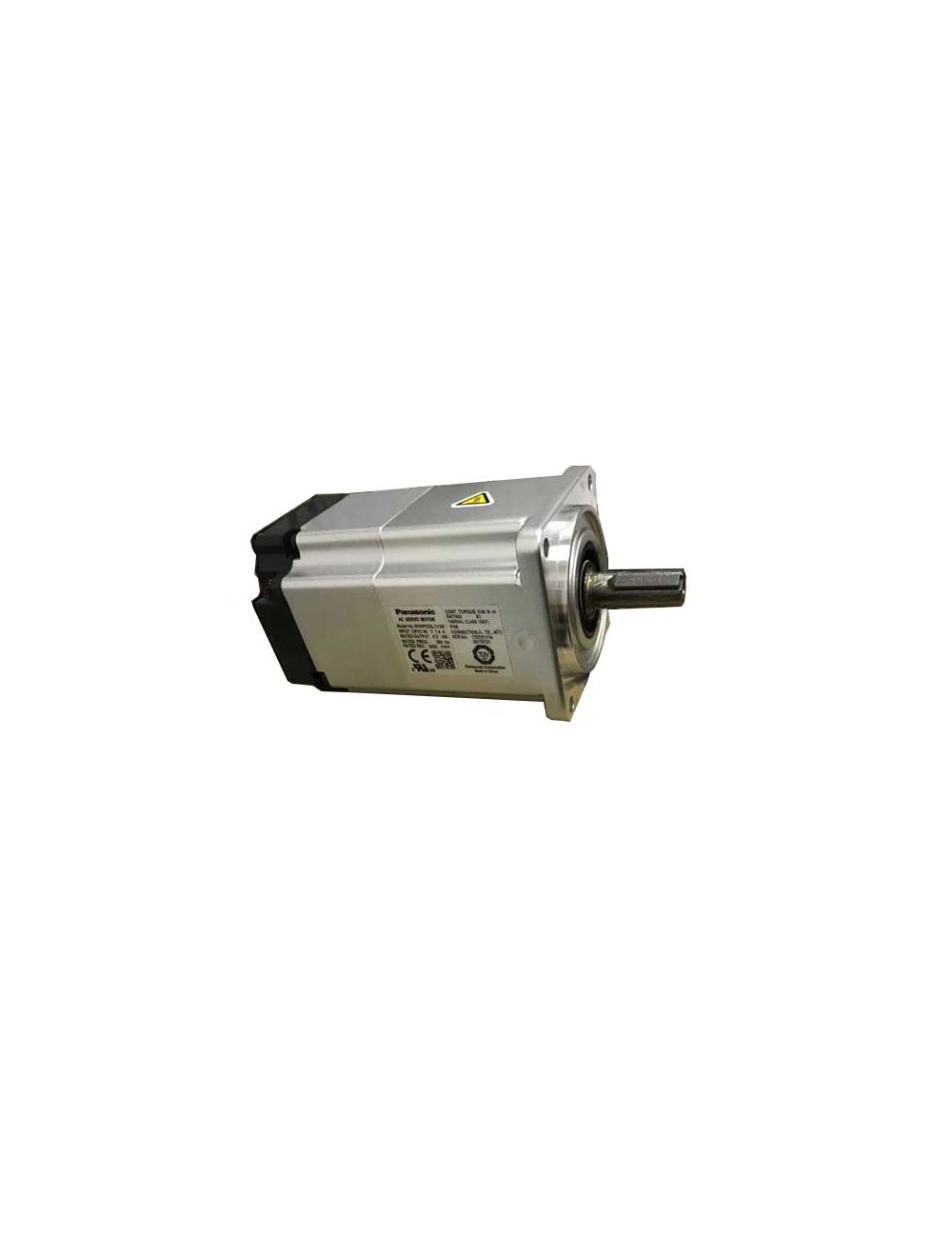
Panasonic Servo Motor MHMF022L1V2M

Honeywell Solenoid Valve VE4025B1045

ROTEN Mechanical Seal 8E5K-22-X

Yaskawa Servo Motor SGMGH-30ACB6S