How many do you know about the essential nine almighties in the bearing industry
1. Installation of bearing
Whether the bearing is installed correctly or not affects the accuracy, life and performance. Therefore, the design and assembly department must fully study the bearing installation. Hope to install in accordance with operating standards. The work standard items are usually as follows:
(1) Cleaning the bearing and its related parts
(2) Check the size and finishing of related parts
(3) Installation
(4) Inspection after bearing installation
(5)Supply lubricant
I hope to open the bearing package just before the installation. General grease lubrication, do not clean, directly filled with grease. Lubricating oil does not need to be cleaned in general. However, the bearings for instruments or high-speed use should be cleaned with clean oil to remove the anti-rust agent coated on the bearings. Bearings with anti-rust agent removed are easy to rust, so they cannot be left alone.
Furthermore, bearings that have been sealed with grease can be used directly without cleaning. The installation method of the bearing varies with the bearing structure, fit and conditions. Generally, since most of the shaft rotates, the inner ring needs an interference fit. Cylindrical bore bearings are usually pressed in with a press or hot-fitting method. In the case of a tapered hole, install it directly on the tapered shaft or use a sleeve.
When installed on the shell, there is generally a large amount of clearance fit and interference in the outer ring. It is usually pressed in with a press, or there is a shrink fit method for installation after cooling. When dry ice is used as the coolant, the moisture in the air will condense on the surface of the bearing when the shrink fit is installed. Therefore, appropriate anti-rust measures are required.
2, bearing material
The rings and rolling elements of rolling bearings are subjected to high contact pressure repeatedly while making rolling contact with sliding. The cage is in sliding contact with the two sides of the ring and the rolling element or one side, and bears the tensile and compressive forces on the other. Therefore, the main requirements for the materials and performance of bearing rings, rolling elements and cages are as follows:
(1) The required properties of ferrule and rolling element materials: high rolling fatigue strength, high hardness, and high wear resistance;
(2) The required performance of the cage material: good dimensional stability and high mechanical strength.
(3) Good workability is required. Depending on the application, it is also required to have good impact resistance, heat resistance, and corrosion resistance.
Material of ferrule and rolling element
Rings and rolling elements usually use high carbon chromium bearing steel. Most of the bearings use SUJ2 in JIS steel grade. SUJ3 is used for large bearings. The chemical composition of SUJ2 has been standardized as a bearing material in countries around the world. For example: AISL52100 (USA), DIN100Cr6 (West Germany), BS535A99 (UK), etc. are all of the same kind of steel.
When further impact resistance is required, chromium steel, chromium-molybdenum steel, nickel-chromium-molybdenum steel are used as bearing materials, and carburizing and quenching are used to make the steel have a hardened layer from the surface to an appropriate depth. Carburized bearings with proper hardening depth, fine structure, proper hardness of surface and core hardness have better impact resistance than bearings using bearing steel, and the chemical composition of general carburized bearing steel. NSK and DKF have implemented vacuum degassing treatment, so the materials used have high purity, low oxygen content, and good quality.
In turn, proper heat treatment is adopted to significantly increase the rolling fatigue life of the bearing. In addition to the above-mentioned steel grades, high-speed steel with excellent heat resistance and stainless steel with good corrosion resistance are also used for special purposes.
cage material
The material of the stamping cage is low carbon steel. Depending on the application, brass plates and stainless steel plates are also used. The material for cutting the cage is made of high-strength brass, carbon steel, and synthetic resin.
3. Storage of bearings
The storage of bearings must first fully consider the size and weight of the stored bearings, and secondly, consider the necessary handling space and equipment to ensure that the bearings will not collide during storage and retrieval. Do not place the bearing directly on the ground.
Therefore, it is necessary to configure a proper shelf, and the bottom of the shelf should be 30cm above the ground. In the general packaging state, the rust prevention effect is 13 years depending on the storage environment. In special circumstances that require storage for nearly 10 years, the storage method can be immersed in oil such as turbine oil (as bearing lubricant).
(1) Work to install bearings
There are many ways to install the bearing, and the same work will be done after installation. After the bearing is installed, the outer ring must be obliquely coated with bearing lubricant.
A. Application of lubricant
1. For grease lubrication, apply lubrication to cover all the roller surfaces, and restore the position of the outer ring after finishing.
2. For oil lubrication, coat all roller surfaces with oil, and restore the position of the outer ring after coating.
B. After coating, cover with plastic film to prevent dust.
(2) Precautions for disassembling the bearing
The disassembly of the bearing is carried out when the bearing needs to be replaced due to regular maintenance or abnormal operation. When the bearings need to be replaced frequently during regular maintenance, the reason for the abnormality should be understood when the bearing is disassembled to prevent the abnormality from recurring. At least the following items should be retained.
1. Collect and keep the used lubricant.
2. Keep damaged bearings.
3. Keep records of abnormal events during operation.
4. Keep a record of the bearing condition during abnormal operation.
4. Maintenance of bearings
In order to make the bearing fully play and maintain its due performance for a long time, it is necessary to do regular maintenance. Through appropriate regular inspections, it is very important to improve productivity and economy to detect faults early and prevent accidents before they occur.
(1) cleaning
When removing the bearing for inspection, first make a record of the appearance with photography or other methods. In addition, confirm the amount of remaining lubricant and sample the lubricant before cleaning the bearing.
The cleaning of the bearing is divided into rough washing and fine washing, and a metal grid can be placed at the bottom of the container in use. For rough washing, use a brush to remove grease or adhesions in oil. If you rotate the bearing in oil at this time, be careful that the rolling surface may be damaged by foreign matter. Slowly rotate the bearing in oil during fine washing and proceed carefully. Commonly used cleaning agents are neutral non-water-containing diesel or kerosene, and mild alkaline liquids are sometimes used as needed. But no matter what kind of cleaning agent is used, it must be filtered frequently to keep it clean. After cleaning, immediately apply anti-rust oil or anti-rust grease on the bearing.
(2) Inspection and judgment
In order to judge whether the removed bearing can be reused, it is necessary to check its dimensional accuracy, rotation accuracy, internal clearance, mating surface, raceway surface, cage and seal ring. Regarding the inspection results, it can be judged by those who use inertial bearings or are proficient in bearings. Judgment criteria vary according to mechanical performance and importance, inspection cycle, etc. If the following damage occurs, the bearing must not be reused and must be replaced.
5. Adjustment of bearing axial clearance
The axial clearance inside the bearing can be achieved by moving the axial position of the outer ring.
1 Adjusting shim method
Fill a set of soft material (soft steel or elastic paper) gaskets between the bearing end cover and the end surface of the bearing seat; when adjusting, first install the bearing end cover without placing the gasket, and tighten the bearing end cover evenly on the same side. Screw, while turning the shaft by hand, until the bearing rolling element is in contact with the outer ring and there is no gap inside the shaft; at this time, measure the gap between the bearing end cover and the end surface of the bearing seat, plus the shaft required by the bearing in normal operation Toward the gap; this is the total thickness of the gasket to be filled, and then fill the prepared gasket between the bearing end cover and the end face of the bearing seat, and tighten the screws after z*.
2 Adjusting bolt method
Press the pressure ring on the outer ring of the bearing and pressurize with the adjusting bolt; before the pressure adjustment, first measure the pitch of the adjusting bolt, and then slowly tighten the adjusting bolt until there is no gap in the bearing, and then calculate the adjustment The corresponding rotation angle of the bolt. For example, if the pitch is 1.5mm, the clearance required for the normal operation of the bearing, then the required rotation angle of the adjusting bolt is 3600×0.1535=360; at this time, if the adjusting bolt is reversed 360, the bearing will obtain an axial clearance of 0.5mm , And then fix it with a stop washer.
6. Bearing damage and countermeasures
Bearing damage
Generally, if the bearing is used correctly, it can be used until the fatigue life is reached. However, there may be accidents that are prematurely damaged and cannot withstand use. This kind of early damage, as opposed to fatigue life, is the quality limit called failure or accident. It is mostly caused by careless installation, use, and lubrication, foreign matter invaded from the outside, and insufficient research on the thermal effect of the shaft and housing.
About the damage state of the bearing
The jamming of the ring and rib of the roller bearing can be considered as the cause. There may be insufficient lubricant, unsuitability, defects in the oil supply and drainage structure, foreign matter intrusion, bearing installation errors, and excessive shaft deflection. These reasons coincide. Therefore, it is difficult to know the real cause of the damage only by investigating bearing damage. However, if you know the bearing's operating machinery, operating conditions, the structure around the bearing, understand the situation before and after the accident, combined with the damage state of the bearing and several reasons, you can prevent similar accidents from happening again.
7, bearing form
Inch single row deep groove ball bearing: R
Inch single row deep groove ball bearing with flange: FR
Metric single row deep groove ball bearing: The symbol is omitted
metric single row deep groove ball bearing with flange: F
Metric single row deep groove ball bearings of specific size: MR
Specific size metric single row deep groove ball bearing with flange: MF
Thrust bearing with groove: FM
Trackless thrust bearing: F
Sealing ring. Dust cover
Contact type Teflon seal with retaining ring on both sides: TT
Steel plate dust cover on both sides: ZZ
Contact rubber seals on both sides: 2RS
8. Selection of rolling bearing oil
Spindle bearing lubricants that use rolling bearings are generally considered based on the product of the bearing inner diameter d and the spindle speed n, that is, the speed factor dn, the bearing operating temperature T, and the load P borne by the bearing. The variety of lubricating oil can be selected from Japan Central Oil Chemical (COC) high temperature grease bearing oil, which can be determined according to product variety, working conditions and viscosity grade.
Bearing working temperature -30-0℃, normal load (3MPa) suitable oil viscosity (40℃) 18-32mm2/s, viscosity grade 22, 32; heavy load or shock load (3MPa-20MPa) suitable oil viscosity (40℃) ) 18-50mm2/s, viscosity grade 32, 46.
Bearing operating temperature 0-60℃, speed factor (dn value) below 15000mm.r/min, normal load suitable oil viscosity (40℃) 32-70mm2/s, viscosity grade 32, 46, 68, heavy load or impact load (3MPa-20MPa) Applicable oil viscosity (40℃) 70-192mm2/s, viscosity grade 68, 100, 150;
Speed factor (dn value) 15000-75000mm.r/min, normal load suitable oil viscosity (40℃) 32-50mm2/s, viscosity grade 32, 46, heavy load or impact load (3MPa-20MPa) suitable oil viscosity ( 40℃) 42-90mm2/s, viscosity grade 46, 68, 100;
Speed factor (dn value) 75000-150000mm.r/min, normal load suitable oil viscosity (40℃) 15-32mm2/s, viscosity grade 15, 32, heavy load or impact load (3MPa-20MPa) suitable oil viscosity ( 40℃)32-42mm2/s, viscosity grade 32; speed factor (dn value) 150000-300000mm.r/min, normal load suitable oil viscosity (40℃) 9-12mm2/s, viscosity grade 5, 7, 10, Heavy load or shock load (3MPa-20MPa) is suitable for oil viscosity (40℃) 18-32mm2/s, viscosity grade 15.
Bearing operating temperature 60-100℃, speed factor (dn value) below 15000mm.r/min, normal load suitable oil viscosity 40℃110-192mm2/s (100℃9.3-12.5mm2/s), viscosity grade 150, heavy load Or impact load (3MPa-20MPa), suitable for oil viscosity (40°C) 195-240mm2/s (100°C 15-24mm2/s), viscosity grade 150;
Speed factor (dn value) 15000-75000mm.r/min, normal load suitable for oil viscosity 40℃70-120mm2/s (100℃5.6-9.3mm2/s), viscosity grade 68, 100, heavy load or impact load ( 3MPa-20MPa) suitable oil viscosity (40℃) 110-192mm2/s, viscosity grade 150; speed factor (dn value) 75000-150000mm.r/min, normal load suitable oil viscosity 40℃50-90mm2/s(100℃ 5.6-9.3mm2/s), viscosity grade 46, 68, 100, heavy load or shock load (3MPa-20MPa) suitable for oil viscosity (40℃) 70-120mm2/s, viscosity grade 100.
9. Matters needing attention in measuring bearing radial clearance
(1) As far as possible, use special instrument measurement methods.
(2) The use of hand-pushing measurement requires the measurer to have high measurement skills. The measurement error of this method is relatively large, especially when the clearance is in the edge state, it is easy to cause errors. At this time, the instrument measurement shall prevail.
(3) When measuring with a feeler gauge, the operation should be carried out according to the provisions of the standard, and the method of rolling over the feeler gauge with a roller is not allowed to measure.
(4) During the measurement process, the ball should be ensured to fall into the bottom of the groove, and the closed bearing should be measured before closing. When a loaded instrument is used, the measured value should also deduct the increase in clearance caused by the load.
(5) For multi-row bearings, the clearance of each row is required to be qualified, and the arithmetic average of the clearances of each row is taken as the radial clearance of the bearing.
How many do you know about the essential nine almighties in the bearing industry
Recent related posts
09/04/2020
How many do you know about the essential nine almighties in the bearing industry
1. Installation of bearing Whether the bearing is installed correctly or not affects the accuracy, life and performance. Therefore, the design and assembly department must fully study the bearing installation. Hope to install in accordance with operating standards. The work standard items are usually as follows:
09/04/2020
How are commonly used filters classified
The impurities contained in the compressed air of the pneumatic system are divided into four categories: solid dust, moisture, oil mist and odor. In order to meet the requirements of different industrial sectors on the quality of compressed air,
09/04/2020
Have you heard of the 6S management of the compressor station on-site
For compressor users, on-site management is one of the daily management content of each enterprise.
09/04/2020
Have you considered these four questions when using screw air compressors
When using a screw air compressor, have you considered these four issues: the speed of the screw air compressor, the working temperature of the screw air compressor, the lubrication method of the screw air compressor, and the use environment of the screw air compressor.
09/04/2020
Graphic-the structure of air compressor
An air compressor is an air compressor. It is a device that provides compressed air to various workshops in the factory. It compresses the atmospheric air sucked in from the outside through mechanisms such as screws and bolts
09/04/2020
From the buying habits of motor users, how to better promote high-efficiency motors
Motor energy saving is a key project in industrial energy saving, and the motor system energy saving project is also one of the key energy saving projects designated by my country.
09/04/2020
Factors affecting the use of oil-free air compressors
The oil-free air compressor is the main body of the air source device. It is a device that converts the mechanical energy of the prime mover into gas pressure energy and is a pressure generating device for compressed air. The factors that affect its use are:
09/04/2020
Experts teach you to distinguish six major misunderstandings in the installation and use of inverters and their countermeasures
Today we introduce the six major misunderstandings and countermeasures in the installation and use of inverters. frequency converter
09/04/2020
Energy-saving space of screw air compressor itself
When we talk about the energy saving of screw air compressors, we often start from the outside of the air compressor, such as frequency conversion transformation, waste heat recovery, etc.
09/04/2020
Eight core issues warn compressor companies, and the rapid changes in the market cannot be ignored
When we find that the hot companies a few years ago have become traditional enterprises, you will understand how fast we are in an era of change! Most compressor companies now have a very serious sense of crisis-dealers are difficult to manage
Customers frequently viewed

IWAYA DENKI Water Pump 25CJT0752
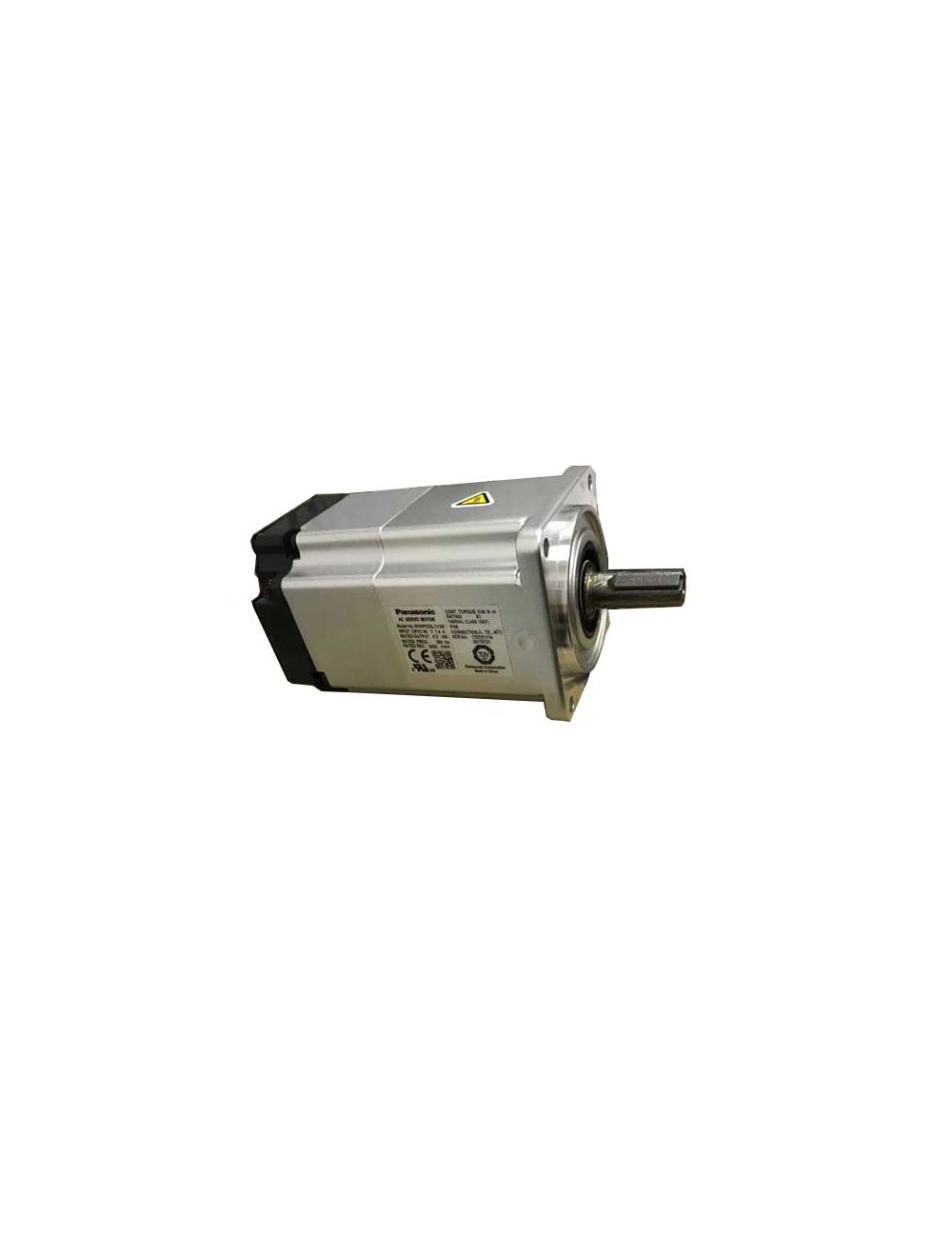
Panasonic Servo Motor MHMF022L1V2M

Honeywell Solenoid Valve VE4025B1045

ROTEN Mechanical Seal 8E5K-22-X

Omron Switch V-163-1A5
TAIAN Relay RHU-10M/8d0 3.5-4.8A/6de