With the continuous development of modern textile technology, compressed air has been widely used. Compressed air in the textile industry is used in pneumatic pressurization, pneumatic weft insertion, air jet twisting, pneumatic humidification, air conveying, air cleaning, pneumatic doffing, and instrument automatic control. Among them, the power source of the air jet loom is compressed air as the carrier for weft insertion, which consumes a lot of compressed air, and the pressure and quality requirements of the compressed air are particularly strict. The compressed air production process is a high energy consumption process, so the air compressor system becomes a high energy consumption part. In-depth understanding of textile mills’ requirements for compressed air quality, determination of air consumption at each point of use, correct selection of air compressors (referred to as air compressors), reasonable design of compressed air stations and compressed air pipe networks, to ensure normal textile production and save Energy is particularly important.
State parameters and quality of textile compressed air
1. Compressed air state parameters
2. After air is compressed, its pressure and temperature increase, and its saturated moisture content decreases. Therefore, the main state parameters of compressed air are pressure, temperature, moisture content, etc., and their meaning and mutual conversion relationship conform to the law of engineering thermodynamics.
3.1) Pressure and temperature
Due to the needs of process production, the pressure has different requirements, and the unit is expressed in MPa in engineering. As the temperature of the compressed air increases, it needs to be cooled to meet the requirements before being sent to the workshop.
2) The moisture content of the air
3) At a certain temperature and pressure, the content of water vapor in humid air has a maximum value. When this limit is reached, excess water vapor will be released from the humid air. The humid air with the maximum water vapor content at a certain temperature is called saturated air. The moisture content of the air at this time is called the saturated moisture content. The saturated moisture content is related to the temperature and pressure of the humid air. When the pressure of compressed air increases and the temperature decreases, its saturated moisture content will decrease, and vice versa. For example, assuming that the temperature of the humid air before and after compression is 30°C, when the pressure increases from 0.1 MPa to 0.8 MPa, the saturated moisture content of the humid air will decrease from 27.55 g/kg to 3.22 g/kg. It can be seen that when the wet air is compressed, its saturated moisture content is greatly reduced. The wet air that did not reach saturation may reach saturation and a large amount of water will be analyzed and condensed in the compressed air pipeline system. Therefore, the compressed air system must properly collect and remove condensate and solve the problem of drying of compressed air.
4) Under a certain pressure, the temperature at which the compressed air is cooled to saturation is called the pressure dew point temperature of the compressed air, so the pressure dew point temperature of the compressed air corresponds to the moisture content. In the compressed air drying process, the moisture content of the compressed air is usually processed below the dew point temperature of a certain pressure. In use, as long as the temperature of the compressed air is not lower than its dew point temperature, no water will be analyzed. Therefore, the pressure dew point temperature is often used in engineering to express the dryness of the compressed air.
3) Pressure dew point 2. The quality of compressed air Compressed air for textiles due to technological production needs, in addition to certain requirements for compressed air pressure, the quality of compressed air (dust content, water content, oil content) is also relatively High demands. Therefore, the quality of compressed air is also one of the basis for choosing air compressors and supporting purification equipment.
1) Classification of compressed air quality grades Air quality grades can be classified according to the internationally accepted grade standard ISO 8573-1 air quality grade standard.
3. Requirements for compressed air quality in each process of textile 1. Air-jet loom requirements for compressed air quality Compressed air is the power carrier for weft insertion of air-jet looms. In order to ensure the normal execution of jet weft insertion and the quality of the fabric surface, there must be strict regulations on the quality and pressure of the compressed air.
(1) The oil content of the air. The compressed air used for jet weft insertion must not contain oil or very little oil. If the compressed air contains oil, it will not only contaminate the fabric, but also stick to the nozzles and reeds, which will affect the jetting force and increase the resistance of weft insertion, making the weft insertion worse. In addition, oily air will pollute the air environment between vehicles and endanger human health. Therefore, the oil content in the compressed air must be strictly limited, and the oil content is generally required; 0.6mg/m3. This requirement is level 2 in the ISO 8573-1 air quality standard.
(2) Air moisture content. Undried compressed air contains a certain amount of water, and its content depends on the amount of water vapor in the humid air in the natural environment before being sucked into the compressor, which varies with the region, season and climatic conditions. If the amount of water vapor in the humid air is large, it will cause the compressed air to precipitate moisture in the pipeline, cause the pipe wall to rust and adhere to dust, increase the pressure loss of the air; it will also cause pollution to the nozzles, reeds and parts of the loom And rust, and even affect the quality of the fabric. Therefore, the compressed air must be dried. Generally, the pressure dew point temperature of compressed air is required to be 4~10℃, which means it can reach the 4th level in the ISO 8573-1 air quality standard.
(3) The amount of dust in the air. Unclean air will accelerate the wear of the compressor, affect the efficiency and life of the loom, and contaminate the cloth surface. The dust content of compressed air is usually required; 1mg/m3, dust particle size; 3~5mu; m, that is, it reaches the second level of the ISO 8573-1 air quality standard.
(4) Pressure requirements. The compressor discharge pressure of compressed air for general air jet looms is determined as follows: compressed discharge pressure; loom initial pressure; loom weft insertion pressure compressor discharge pressure and loom specifications, fabric types, loom rotation The number is related to the boot method. Usually, the initial pressure of the loom is 0.5MPa, the compressor discharge pressure is 0.6MPa, and the compressor specification is 0.7MPa discharge pressure. In order to ensure the normal weft insertion and fabric quality of the air-jet loom, the compressed air pressure must be stable, and the pressure entering the air-jet loom should usually be 0.5MPa.
4. Requirements for compressed air quality in other parts. With the improvement of textile equipment automation and modern textile technology, compressed air has been widely used as a power source. In addition to air-jet looms, in the spinning department And the preparation workshop is mainly used for pneumatic pressurization, pneumatic doffing, air jet twisting, air jet twisting, air jet cleaning and other parts. Except for pneumatic pressure and pneumatic doffing, the above parts have relatively low requirements for compressed air quality (not higher than ISO 8573-1 standard 4), and the other parts are in contact with the yarn. The quality requirements should be the same as that of the air jet loom The quality requirements are the same. For places with pneumatic pressure, the compressed air pressure is generally required to be 0.6~0.8MPa higher than that of air jet looms.
5. Comparison of performance between screw type and centrifugal type When selecting an air compressor in a textile factory, it should be based on the air compressor's exhaust volume and exhaust pressure requirements, with high efficiency, low energy consumption, simple operation and maintenance, and reasonable price. Factors are the main candidates. In order to ensure the quality of textile products, the purification requirements of compressed air (ie, no water, oil and dust) must also be considered. In addition, the air compressor is required to have good adjustment characteristics and energy-saving effects when adjusting the air volume. Only by comprehensively analyzing the above-mentioned problems and taking all factors into consideration can the best selection scheme be determined.
At present, screw air compressors and centrifugal air compressors are used more frequently. Compared with the two, the main advantages of screw compressors are: uniform air intake and exhaust, no pressure pulsation, stable operation of the machine, no need to set up air storage tanks, foundation It can even be operated without a basis; the fuel injection screw can obtain a higher single-stage pressure ratio (up to 20-30) and a lower exhaust temperature; it has the characteristics of forced air delivery, that is, the exhaust volume is hardly affected. The influence of the exhaust pressure, the pressure ratio is basically independent of the speed and density, and it is especially suitable for parallel operation of multiple machines. The disadvantages are: poor air quality, high oil content, easy to cause damage to the equipment; high noise, noise reduction measures must be taken; the exhaust volume is small compared with the centrifuge.
The main advantages of centrifugal air compressors are: compact structure, light weight, large single machine displacement; pure oil-free operation, compressed air is not polluted by lubricating oil, high quality; high efficiency and energy saving. The air quality reaches the level 1 standard (the international general standard ISO8573-1 for air quality). The disadvantage is that it is prone to surging and vibration during starting and stopping. It is not advisable to use multiple units to operate in parallel. When the exhaust capacity and exhaust pressure of a single unit can meet the requirements, it is advisable to select fewer units for air supply.
The air-consumption characteristics of air-jet looms in textile mills are stable flow, low pressure (P; 0.7MPa) and stable air pressure (△P0.01MPa). Therefore, there are more cloth machines, large compressed air consumption and air pressure. Centrifugal compressors should be used in places with low and stable air consumption;
When choosing a centrifugal air compressor, the following general principles should also be followed.
(1) The discharge volume and discharge pressure of the compressor should meet the technological requirements. Due to changes in climatic conditions or fluctuations in air load, the compressor's discharge volume and discharge pressure will also change accordingly. Therefore, the compressor does not always run at a fixed operating point, but runs in a certain operating area. When selecting a compressor, try to make the compressor's operating condition area included in the effective use range of its characteristic curve.
(2) The efficiency of the compressor determines the economy of its normal operation. Therefore, the unit with high rated (designed) efficiency and a wide range of high efficiency should be selected as far as possible.
(2) When the operating conditions change greatly, a unit with good regulation performance and reliable safety protection system should be selected.
(4) When the load is relatively stable and the exhaust volume and exhaust pressure of a single unit can meet the requirements, a single unit should generally be used for air supply.
(5) On the premise of meeting the gas supply requirements, strive to be small in size, light in weight, reduce floor space, facilitate maintenance and repair, and save investment.
(6) In the following cases, it is advisable to use multiple units to supply air in parallel. When the load changes greatly and it is difficult for a single unit to adapt to the adjustment conditions; when the gas supply must be increased without renewing the existing compressor; when the gas demand is large, when the size of a compressor is too large or there are difficulties in manufacturing .
Compressors working in parallel can use units with the same performance specifications or units with different performance specifications; the former is widely used due to the better coordination between the units, and the latter is only suitable for large load changes. When it is necessary to start the auxiliary unit to work together, the exhaust pressure of the parallel unit must be equal or substantially equal regardless of the displacement.
When choosing a centrifugal air compressor and determining its operating parameters, attention should be paid to the impact of anti-surge conditions and blocking conditions, and the stable working area of the centrifugal compressor should be determined.
The centrifugal air compressor is driven by the impeller to rotate the gas at high speed, so that the gas generates centrifugal force. Due to the diffused flow of the gas in the impeller, the flow rate and pressure of the gas after the impeller are increased, and compressed air is continuously produced.
The centrifugal air compressor is a speed compressor, and the centrifugal air compressor works stably and reliably when the air load is stable.
①Compact structure, light weight, large displacement range;
② Few wearing parts, reliable operation and long life;
③The exhaust gas is not polluted by lubricating oil, and the air supply quality is high; ④The efficiency is high when the displacement is large, and it is conducive to energy saving.
Working principle of centrifugal air compressor
The centrifugal air compressor is mainly composed of the rotor and the stator. The rotor includes an impeller and a shaft. There are blades on the impeller, in addition to the balance disc and part of the shaft seal. The main body of the stator is the casing (cylinder), and the stator is also arranged with a diffuser, a curve, a reflux device, an air pipe, an exhaust pipe, and a partial shaft seal. The working principle of the centrifugal compressor is that when the impeller rotates at a high speed, the gas rotates with it. Under the action of centrifugal force, the gas is thrown into the diffuser behind, and a vacuum zone is formed at the impeller. At this time, the outside fresh gas Enter the impeller. The impeller continuously rotates, and the gas is continuously sucked in and thrown out, thereby maintaining a continuous flow of gas.
Centrifugal air compressors rely on changes in kinetic energy to increase gas pressure. When the rotor with blades (that is, the working wheel) rotates, the blades drive the gas to rotate, transfer work to the gas, and make the gas obtain kinetic energy. After entering the stator part, the speed energy pressure head is converted into the required pressure due to the pressure diffusion action of the stator. The speed decreases and the pressure rises. At the same time, it uses the guiding action of the stator part to enter the next stage of the impeller to continue to increase the pressure, and finally is discharged by the volute. . For each compressor, in order to achieve the design required pressure, each compressor has a different number of stages and stages, and even consists of several cylinders.
The use of centrifugal air compressors for texturing machines, air-jet looms, and front spinning in the textile industry saves 15% of the cost of purchasing compressed air.
Is it the best companion for air-jet looms Centrifugal air compressor saves energy consumption by 30%!
Recent related posts
08/27/2020
Is it the best companion for air-jet looms Centrifugal air compressor saves energy consumption by 30%!
With the continuous development of modern textile technology, compressed air has been widely used. Compressed air in the textile industry is used in pneumatic pressurization, pneumatic weft insertion, air jet twisting,
08/27/2020
How to maintain your oil-free screw compressor
Like all electromechanical equipment, oil-free screw compressors require regular maintenance to operate at maximum efficiency and minimize unplanned downtime. Improper maintenance can cause problems such as reduced compression efficiency, air leakage, and pressure changes.
08/27/2020
Do you know the distress signal of screw air compressor
The screw air compressor will inevitably have various problems during long-term use, and an alarm will be triggered at this time. Especially in the high temperature in summer, screw air compressors are more likely to appear frequently.
08/27/2020
Brief Discussion on Monitoring of Safety Protection Device of Mine Air Compressor
In the process of monitoring and inspecting the safety of air compressors in mining enterprises, the author found that more than 90% of the equipment was not equipped or not fully equipped with the temperature and pressure protection devices that should be configured.
08/27/2020
Analysis and Improvement of Broken Shaft of Main Oil Pump of Centrifugal Compressor
I. Introduction<br></br> CNOOC Dongfang Petrochemical's air compressor station installation provides non-purified air and clean air for instruments to all production installations and auxiliary facilities of public works throughout the plant. The unit is manufactured by a foreign company, C1000 series <br></br>
08/27/2020
Design and Application of Universal Crank and Connecting Rod Mechanism
First, let me introduce the function of the crank connecting rod mechanism to the internal combustion engine: 1) convert heat energy into mechanical energy; 2) piston reciprocating linear motion becomes crankshaft rotation motion; 3) output continuous power to related transmission devices.
08/27/2020
Compressor overhaul and correct installation matters, super complete and detailed
Content covered by compressor overhaul Compressors generally need to be overhauled after 12,000-26,000 hours of operation. In addition to all the work required for intermediate maintenance,
08/27/2020
A huge energy saving space in the air compressor system that should not be ignored
In recent years, the energy-saving transformation of air compressors has been carried out in full swing. Compared with ordinary power frequency air compressors,
08/27/2020
How to prevent the oil-free scroll air compressor from overheating in hot summer days
The high temperatures in the hot summer days are particularly prone to machine shutdowns and even spontaneous combustion. Compressed air is an indispensable part of the daily operations of many companies.
08/27/2020
Analysis and Improvement of Broken Shaft of Main Oil Pump of Centrifugal Compressor
2. CNOOC Dongfang Petrochemical's air compressor station installation provides non-purified air and clean air for instruments to all production installations and auxiliary facilities of public works throughout the plant.
Customers frequently viewed

IWAYA DENKI Water Pump 25CJT0752
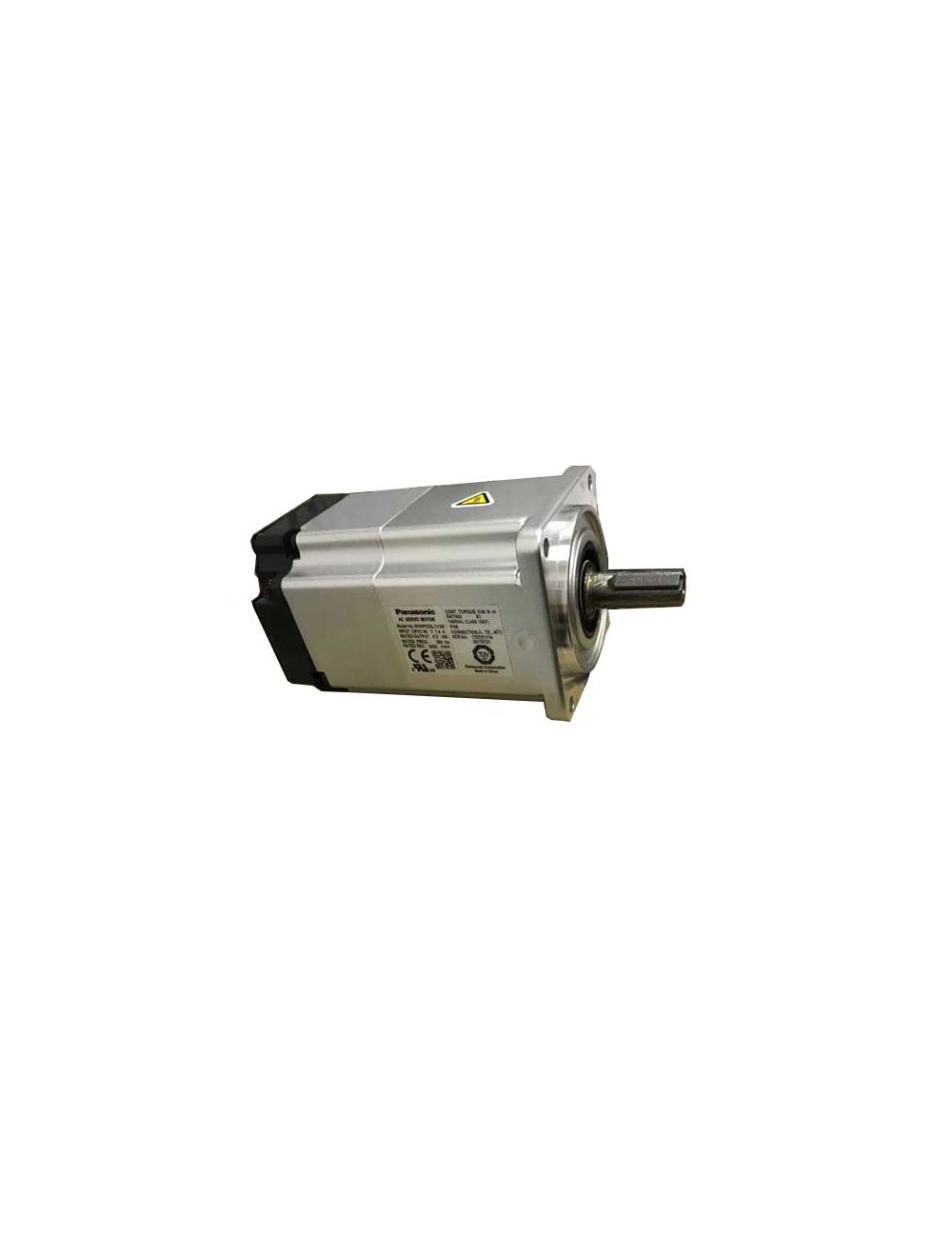
Panasonic Servo Motor MHMF022L1V2M

Honeywell Solenoid Valve VE4025B1045

ROTEN Mechanical Seal 8E5K-22-X

Protechnic Fan MGT4024XB-R10

Daikin Air Conditioner FQRAP18DAPN

AirTAC Air Cylinder SE50X25S