
The principle of centrifugal compressor structure

Recent related posts
06/21/2020
The principle of centrifugal compressor structure
The principle of centrifugal compressor structure Structure principle of centrifugal compressor <img src="{{media url="The_principle_of_centrifugal_compressor_structure.jpg"}}" alt="" /> Centrifugal compressor is composed of rotor, stator and bearing. The impeller and other parts are sleeved on the main shaft to form a rotor. The rotor is supported on the bearing and driven by the power machine to rotate at high speed.
06/21/2020
Advantages of rolling rotor compressors_Disadvantages of rolling rotor compressors
Advantages of rolling rotor compressors_Disadvantages of rolling rotor compressors Rolling rotor compressor, also known as rolling piston compressor or fixed vane compressor, is a type of rotary compressor. <img src="{{media url="Advantages_of_rolling_rotor_compressors_Disadvantages_of_rolling_rotor_compressors.jpg"}}" alt="" /> Working principle of rolling rotor compressor Rolling rotor compressor is a volume type rotary compressor. The change of the working volume of the cylinder is achieved by the rolling of the cylindrical rotor of the cylinder in the cylinder by an eccentric device.
06/21/2020
Which is better, semiconductor refrigeration and compressor refrigeration
Which is better, semiconductor refrigeration and compressor refrigeration <img src="{{media url="o4YBAF3LcwuAC1ILAAEzxLDPcHA979.jpg"}}" alt="" />Semiconductor refrigeration Semiconductor refrigerator refers to a device that uses the thermo-electric effect of semiconductor to produce cooling capacity, also known as thermoelectric refrigerator. Connect two different metals with conductors, and connect direct current, then the temperature at one contact will decrease and the temperature at the other contact will increase.
06/21/2020
Will the air compressor explode_The cause and measures of air compressor explosion
Will the air compressor explode_The cause and measures of air compressor explosion Will the air compressor explode <img src="{{media url="Will_the_air_compressor_explode_The_cause_and_measures_of_air_compressor_explosion.jpg"}}" alt="" /> The air compressor will explode. However, air compressors are not easy to explode. The accident rate of the air storage tank of the piston type air compressor is very small. Only when the air pressure switch and the safety valve of the air compressor are broken at the same time will the air compressor have the possibility of explosion.
06/21/2020
Common faults and maintenance of air compressor
Common faults and maintenance of air compressor <img src="{{media url="Common_faults_and_maintenance_of_air_compressor.jpg"}}" alt="" /> Common faults and maintenance of air compressor Air compressors are widely used in various industries with the development of technology, but no matter what type of air compressor, there will be some problems in the process of use. The following editors will now introduce some common faults and maintenance methods, let's take a look.
06/21/2020
Air compressor selection_air compressor parameters
Air compressor selection_air compressor parameters Air compressor selection <img src="{{media url="Air_compressor_selection_air_compressor_parameters.jpg"}}" alt="" /> How to choose an air compressor in a reasonable way should comprehensively consider the comprehensive technical and economic indicators such as the investment and operating costs of the air compressor unit and the air compressor station, so that it conforms to the principles of economy, safety and application. Specifically, there are the following aspects:
06/21/2020
The basic structure of piston compressor_Composition system of piston compressor
The basic structure of piston compressor_Composition system of piston compressor Basic structure of piston compressor <img src="{{media url="The_basic_structure_of_piston_compressor.jpg"}}" alt="" /> Piston refrigeration compressor is mainly composed of body, crankshaft, connecting rod, piston group, valve, shaft seal, oil pump, energy adjustment device, oil circulation system and other components.
06/21/2020
The classification of piston compressor_The advantages and disadvantages of piston compressor Classification of piston compressor
The classification of piston compressor_The advantages and disadvantages of piston compressor <img src="{{media url="The_classification_of_piston_compressor.jpg"}}" alt="" />Classification of piston compressor (1) Classification according to the position of the cylinder centerline Vertical compressor: The center line of the cylinder is perpendicular to the ground. Horizontal compressor: The center line of the cylinder is parallel to the ground, and the cylinder is only arranged on one side of the fuselage.
06/21/2020
[Experience] What happens if the compressor suction pressure is too high and the discharge pressure is too high
[Experience] What happens if the compressor suction pressure is too high and the discharge pressure is too high Compressor suction pressure is too high, discharge pressure is too high 1. Too much refrigerant. Too much refrigerant will cause the suction pressure and discharge pressure to be too high at the same time. This is because when too much refrigerant fills the reservoir, it will occupy a part of the condenser volume, reducing the heat dissipation area and causing the condenser Poor condensation. Discharge excess refrigerant from the low-pressure side.
06/21/2020
Operation process of automobile air-conditioning refrigeration system and the role of pressure switch
Operation process of automobile air-conditioning refrigeration system and the role of pressure switch From top to bottom, automobile air conditioners are mainly composed of blowers, evaporators, pressure switches, dryers, expansion valves, condensers, and the most source compressors. The operation process of this air-conditioning system is: heat dissipation,
Customers frequently viewed

IWAYA DENKI Water Pump 25CJT0752
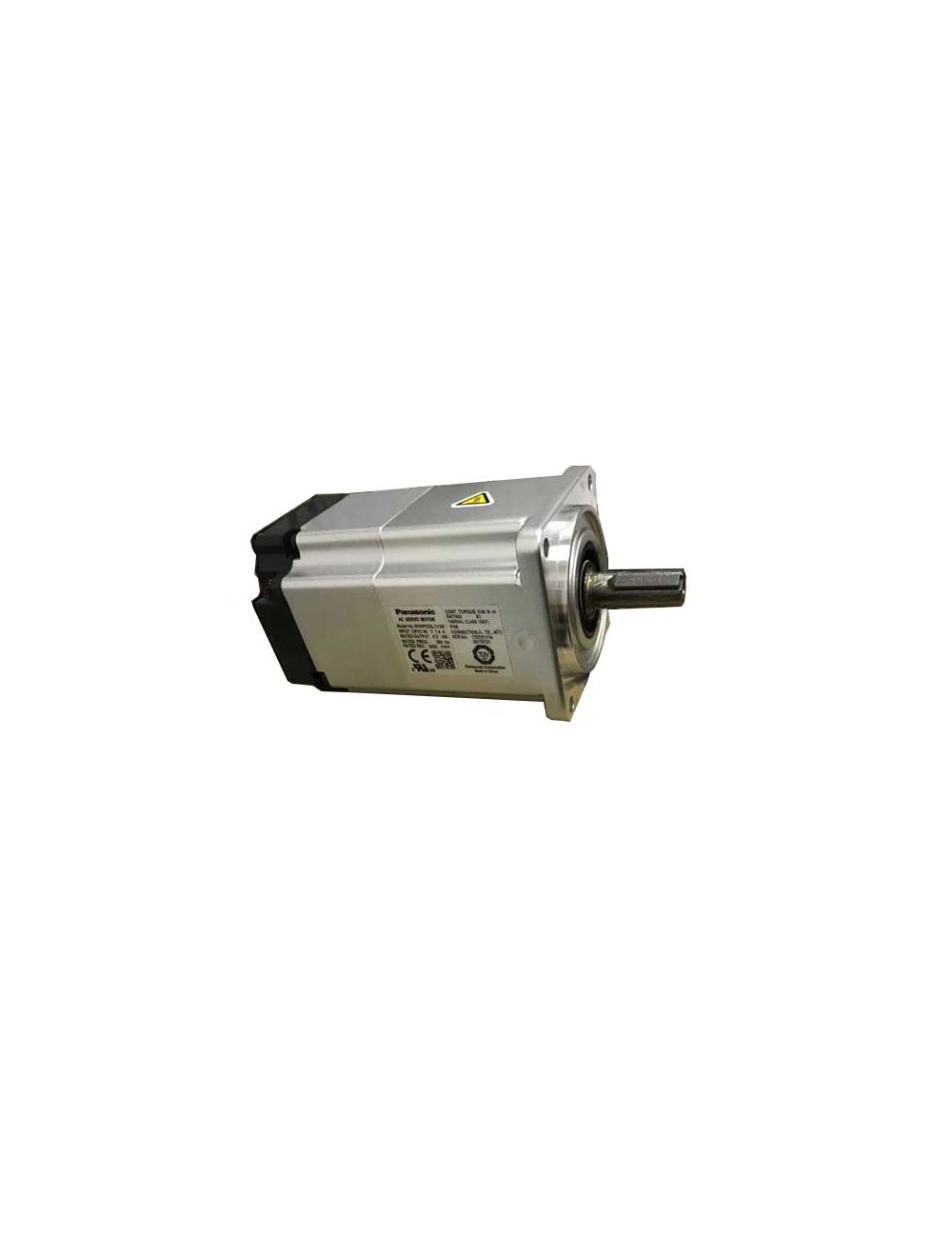
Panasonic Servo Motor MHMF022L1V2M

Honeywell Solenoid Valve VE4025B1045

ROTEN Mechanical Seal 8E5K-22-X

Autonics Sensor PRAT18-5DO

SMC Solenoid Valve SYJ3130-5MZ