
Working principle of sliding vane compressor_Features of sliding vane compressor

Recent related posts
06/20/2020
Working principle of sliding vane compressor_Features of sliding vane compressor
Working principle of sliding vane compressor <img src="{{media url="magefan_blog/Working_principle_of_scroll_compressor_Characteristics_of_scroll_compressor.jpg"}}" alt="" /> Air is sucked in through a filter and a regulating proportional valve. The regulating valve is mainly used to regulate the pressure chamber formed by the rotor and slide of the air cylinder. The rotor rotates eccentrically with respect to the cylinder, the valve plate is installed in the rotor groove, and the slider is pushed to the cylinder wall by centrifugal force.
06/20/2020
The role of condensing pressure regulating valve
Condensing pressure regulating valve When the refrigeration device is running, if the condensing pressure is high, the compressor discharge temperature will rise; the compression ratio will increase; the cooling capacity will decrease; The higher the condensing pressure, the greater the above adverse effects. The high condensation pressure is mainly seen in summer. <img src="{{media url="The_role_of_condensing_pressure_regulating_valve.jpg"}}" alt="" />
06/19/2020
Structure of multi-vane compressor_Characteristics of multi-vane compressor
Structure of multi-vane compressor_Characteristics of multi-vane compressor <img src="{{media url="Structure_of_multi-vane_compressor_Characteristics_of_multi-vane_compressor.jpg"}}" alt="" /> The sliding vane refrigeration compressor is a positive displacement rotary compressor. It can be divided into two types: single slide type and multi slide type. Multi-slider compressors are currently mainly used as low-pressure compressors with two-stage compressors.
06/19/2020
Structure diagram of single vane compressor_Main features of single vane compressor
The basic structure and working principle of single slide compressor.<img src="{{media url="Structure_diagram_of_single_vane_compressor_Main_features_of_single_vane_compressor.jpg"}}" alt="" /> Single sliding vane compressor is also called scraper compressor or rolling rotor compressor. Its structure is shown in Figure 3-7. A cylindrical eccentric rotor (also called a piston) is installed in the cylinder, and the center of rotation of the rotor coincides with the center of the cylinder. In the middle of the upper part of the cylinder, a scraper that can slide up and down is installed. Due to the force of the spring,<img src="{{media url="Structure_diagram_of_single_vane_compressor_Main_features_of_single_vane_compressor2.jpg"}}" alt="" />
06/19/2020
Common fault phenomena, causes and elimination methods of piston compressors
Common fault phenomena, causes and elimination methods of piston compressors Common faults of piston compressor (1) Phenomenon: the compressor cannot start Reasons: 1. Electrical circuit failure; 2. High and medium voltage relay and oil pressure relay are disconnected.<img src="{{media url="Common_fault_phenomena_causes_and_elimination_methods_of_piston_compressors.jpg"}}" alt="" />
06/20/2020
Scroll compressor structure diagram_Scroll compressor advantages and disadvantages
Scroll compressor structure diagram <img src="{{media url="Scroll_compressor_structure_diagram_Scroll_compressor_advantages_and_disadvantages.jpg"}}" alt="" /> Scroll compressor is a positive displacement compression compressor, the compression component is composed of moving scroll and static scroll. Its working principle is to use the relative orbital motion of the movable and static scrolls to form a continuous change in the enclosed volume, so as to achieve the purpose of compressing gas. Mainly used in air conditioning, refrigeration, general gas compression, and used in automobile engine supercharger and vacuum pump, etc., it can replace traditional medium and small reciprocating compressors in a large range. <img src="{{media url="Scroll_compressor_structure_diagram_Scroll_compressor_advantages_and_disadvantages2.jpg"}}" alt="" />
06/19/2020
Working principle of scroll compressor_Characteristics of scroll compressor
Working principle of scroll compressor <img src="{{media url="Working_principle_of_scroll_compressor_Characteristics_of_scroll_compressor.jpg"}}" alt="" /> Scroll compressor is a kind of positive displacement compression compressor, the compression part is composed of movable scroll and static scroll. This includes many structural features that divert the flow of gas through the compressor housing to reduce entrained oil.
06/19/2020
Application advantages and working process analysis of air energy heat pump
Air energy heat pump is to use the energy in the air to generate heat energy. It can provide 24 hours a day with large water volume, high water pressure and constant temperature to provide the family with different hot water, cooling and heating needs, and at the same time can meet the above requirements with the least energy consumption.<img src="{{media url="Application_advantages_and_working_process_analysis_of_air_energy_heat_pump.jpg"}}" alt="" />
06/19/2020
Installation instructions for explosion-proof air conditioners
Installation instructions for explosion-proof air conditioners <img src="{{media url="Installation_instructions_for_explosion-proof_air_conditioners.jpg"}}" alt="" /> 1. The power supply of the explosion-proof air conditioner shall have a dedicated line, and a circuit breaker or air switch shall be provided in the dedicated line. The power supply wires and fuses should comply with the relevant regulations and cannot be changed at will.
06/19/2020
Three common faults and solutions of water-cooled air conditioners
Water-cooled air-conditioning failure 1. Water-cooled air-conditioning noise causes and troubleshooting <img src="{{media url="Three_common_faults_and_solutions_of_water-cooled_air_conditioners.jpg"}}" alt="" /> Water-cooled air conditioners are noisy and often affect the quality of sleep, which leads to irregular life and rest. At this time, the reasons and solutions of water-cooled air conditioner noises need to be considered:
Customers frequently viewed

IWAYA DENKI Water Pump 25CJT0752
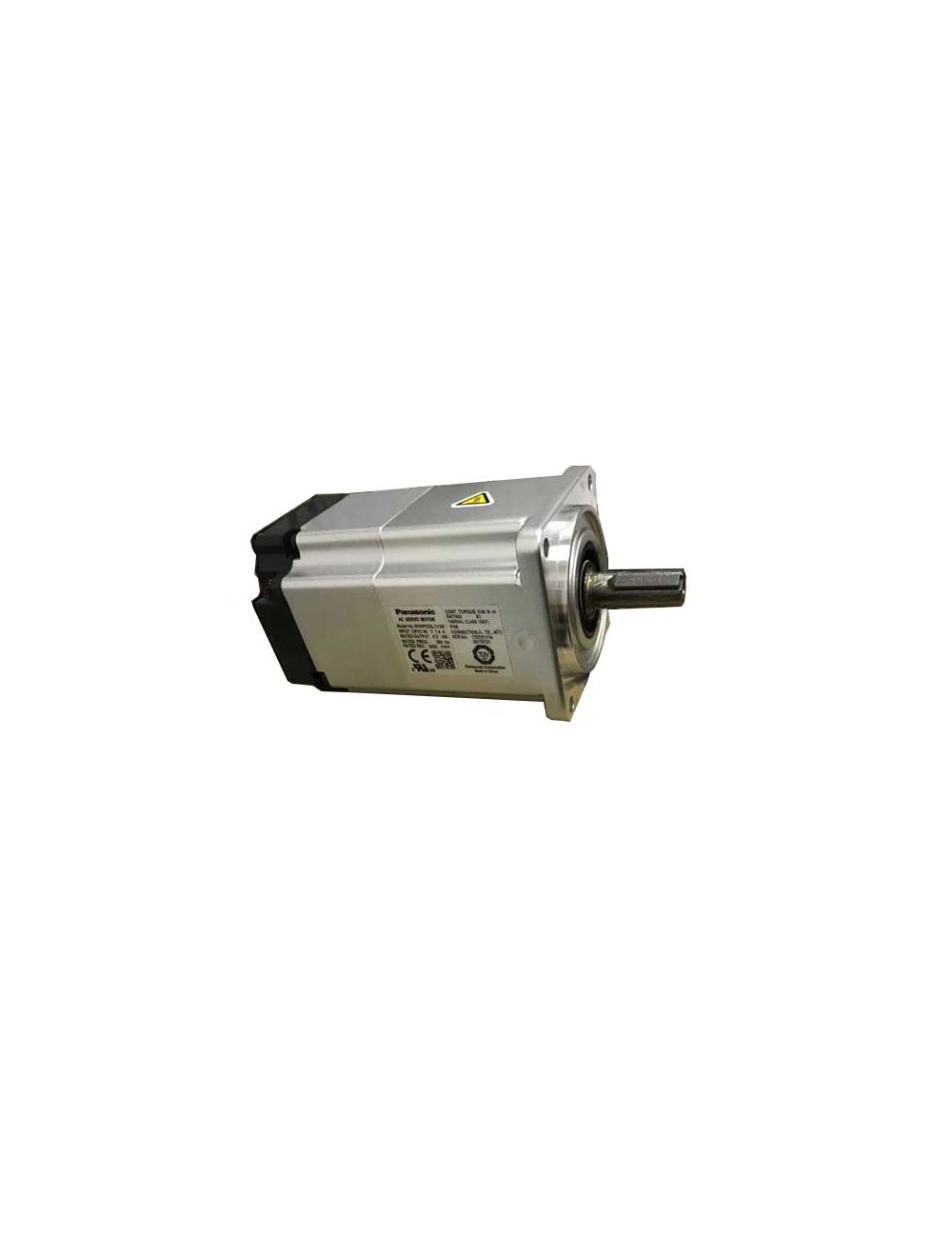
Panasonic Servo Motor MHMF022L1V2M

Honeywell Solenoid Valve VE4025B1045

ROTEN Mechanical Seal 8E5K-22-X

Eaton Contactor DILM9-01(230V50HZ

HENGSTLER Encoder RI58-T/5EG.43KF

Kompass Vane Pump VE2-40F-A2+PA

Delta Fan AFB1212VH