Detailed process of refrigeration compressor replacement
Recent related posts
06/14/2020
Detailed process of refrigeration compressor replacement
Detailed process of refrigeration compressor replacement After confirming that there is only a problem with the compressor and it needs to be replaced, proceed to prepare for the replacement of the compressor. Specific steps are as follows:
06/14/2020
Causes of liquid shock in refrigeration compressors
Causes of liquid shock in refrigeration compressors 1) Too much refrigerant is added to the entire refrigeration system. 2) The throttle valve is opened too large, or the adjustment is malfunctioning. 3) The evaporation area is too sm 器2 䀀 ᅵ皥 䖒皦즠Ʋ煔क़ 㲈Ʋ 䌁皦 ᮔDž༬皧煞क़Ѐ 呄ᠾ鹨់༹皧 ࠄ 00령ꐱ댁珵뛐珵Љ 䕄ྦ 뤂ᐱ뚜珵 ᴴᏩ呄ᠾ퍘ᒥ 鹨់ᩄ ꋔྦ 瑉浥 巠皱㙲皦抐皱 巠皱 ੨皦柘皱 ᅵ皥 ب 巠皱㙲皦忈皱 ੨皦柘皱 즠Ʋǜ 勁皦즠Ʋب ǜ V / 펔B䌁皦 ᮔDž '鱤džၜ먢䇨珵呈ᠾ뤂ᐱ ⿇⬿먲僧ᐱ㥲ᐲ�僬㣢ᐲ ᠾ 랖僧ք 識 �僬㣢ᐲ 臆S㥲ᐲ ᬄğ 識 理艏S杴 識杴 㥲ᐲ
06/14/2020
Disassembly and maintenance of industrial screw refrigeration compressor
Disassembly and maintenance of industrial screw refrigeration compressor 1. Working principle, movement and movement characteristics of screw refrigeration compressor Screw refrigeration compression belongs to volumetric refrigeration compressor. It 器2 䀀 ᅵ皥 䖒皦즠Ʋ嫜ི 㲈Ʋ 䌁皦 ᮔDž༬皧嫦ིЀ 呄ᠾ鹨់༹皧 ࠄ 00령ꐱ댁珵뛐珵Љ 䕄ྦ 뤂ᐱ뚜珵 ᴴᏩ呄ᠾ퍘ᒥ 鹨់ᩄ ꋔྦ 瑉浥 巠皱㙲皦抐皱 巠皱 ੨皦柘皱 ᅵ皥 ب 巠皱㙲皦忈皱 ੨皦柘皱 즠Ʋǜ 勁皦즠Ʋب ǜ V / 펔B䌁皦 ᮔDž '鱤džၜ먢䇨珵呈ᠾ뤂ᐱ
06/14/2020
The specific operation method of screw refrigeration compressor maintenance
Before the screw compressor must be overhauled, if possible, unload the slide valve to the "0" position, shut down normally, and cut off the power supply. The pipeline connected to the compressor should be cut off and the refrigerant and lubricating oil i 器2 䀀 ᅵ皥 䖒皦즠Ʋ煔क़ 㲈Ʋ 䌁皦 ᮔDž༬皧煞क़Ѐ 呄ᠾ鹨់༹皧 ࠄ 00령ꐱ댁珵뛐珵Љ 䕄ྦ 뤂ᐱ뚜珵 ᴴᏩ呄ᠾ퍘ᒥ 鹨់ᩄ ꋔྦ 瑉浥 巠皱㙲皦抐皱 巠皱 ੨皦柘皱 ᅵ皥 ب 巠皱㙲皦忈皱 ੨皦柘皱 즠Ʋǜ 勁皦즠Ʋب ǜ
06/14/2020
An accident analysis of refrigeration compressor
An accident analysis of refrigeration compressor A major refrigerator damage accident occurred in the refrigeration workshop of a meat joint processing plant. The refrigeration workshop of the factory was equipped with 2 single-stage two-stage ammonia re 器2 䀀 ᅵ皥 䖒皦즠Ʋ嫜ི 㲈Ʋ 䌁皦 ᮔDž
06/14/2020
Precautions for use of refrigeration compressor overload protector
The overload protector of the compressor for air-conditioning generally adopts a sudden bimetal protector, which is composed of a heating wire, a bimetal and two static contacts, which are connected in series in the compressor circuit. When the current in 器2 䀀 ᅵ皥 䖒皦즠Ʋ煔क़ 㲈Ʋ 䌁皦 ᮔDž༬皧煞क़Ѐ 呄ᠾ鹨់༹皧 ࠄ 00령ꐱ댁珵뛐珵Љ 䕄ྦ 뤂ᐱ뚜珵 ᴴᏩ呄ᠾ퍘ᒥ 鹨់ᩄ ꋔྦ 瑉浥 巠皱㙲皦抐皱 巠皱 ੨皦柘皱 ᅵ皥 ب 巠皱㙲皦忈皱 ੨皦柘皱 즠Ʋǜ 勁皦즠Ʋب ǜ V / 펔B䌁皦 ᮔDž '鱤džၜ먢䇨珵呈ᠾ뤂ᐱ ⿇⬿먲僧ᐱ㥲ᐲ�僬㣢ᐲ ᠾ 랖僧ۂ 識 �僬㣢ᐲ 臆S㥲ᐲ ᬄğ 識 理艏S杴 識杴 㥲ᐲ
06/14/2020
What to do if the refrigeration compressor is damaged
What to do if the refrigeration compressor is damaged After the refrigeration compressor in the refrigeration system is damaged, the new compressor cannot be replaced directly because there may be some incentives for the refrigeration compressor to be da 器2 䀀 ᅵ皥 䖒皦즠Ʋ嫜ི 㲈Ʋ 䌁皦 ᮔDž༬皧嫦ིЀ 呄ᠾ鹨់༹皧 ࠄ 00령
06/14/2020
Comparison of working principle of single screw and twin screw refrigeration compressors
Comparison of working principle of single screw and twin screw refrigeration compressors 1. Twin screw compressor Twin-screw refrigeration compressor is an energy-adjustable oil-injected compressor. Its three consecutive processes of suction, c 器2 䀀 ᅵ皥 䖒皦즠Ʋ煔क़ 㲈Ʋ 䌁皦 ᮔDž༬皧煞क़Ѐ 呄ᠾ鹨់༹皧 ࠄ 00령ꐱ댁珵뛐珵Љ 䕄ྦ 뤂ᐱ뚜珵 ᴴᏩ呄ᠾ퍘ᒥ 鹨់ᩄ ꋔྦ 瑉浥 巠皱㙲皦抐皱 巠皱 ੨皦柘皱 ᅵ皥 ب 巠皱㙲皦忈皱 ੨皦柘皱 즠Ʋǜ 勁皦즠Ʋب ǜ V / 펔B䌁皦 ᮔDž '鱤džၜ먢䇨珵呈ᠾ뤂ᐱ ⿇⬿먲僧ᐱ㥲ᐲ�僬㣢ᐲ ᠾ 랖僧Ҵ 識 �僬㣢ᐲ 臆S㥲ᐲ ᬄğ 識 理艏S杴 識杴 㥲ᐲ
06/14/2020
Why does the refrigeration compressor frost and the solution!
Why does the refrigeration compressor frost and the solution! 1. The frost on the compressor return air port indicates that the temperature of the compressor return air is too low, so what will cause the compressor return air temperature to be too low? 器2 䀀 ᅵ皥 䖒皦즠Ʋ嫜ི 㲈Ʋ 䌁皦 ᮔDž༬皧嫦ིЀ 呄ᠾ鹨់༹皧 ࠄ 00령ꐱ댁珵뛐珵Љ 䕄ྦ 뤂ᐱ뚜珵 ᴴᏩ呄ᠾ퍘ᒥ 鹨់ᩄ ꋔྦ 瑉浥 巠皱㙲皦抐皱 巠皱 ੨皦柘皱 ᅵ皥 ب 巠皱㙲皦忈皱 ੨皦柘皱 즠Ʋǜ 勁皦즠Ʋب ǜ V / 펔B䌁皦 ᮔDž '鱤džၜ먢䇨珵呈ᠾ뤂ᐱ ⿇⬿먲僧ᐱ㥲ᐲ�僬㣢ᐲ ᠾ 랖僧ӄ 識 �僬㣢ᐲ 臆S㥲ᐲ ᬄğ 識 理艏S杴 識杴 㥲ᐲ
06/14/2020
Basic knowledge of refrigeration compressors! Did you know everything
Basic knowledge of refrigeration compressors! Did you know everything Why should the compressor run continuously for at least 5 minutes, and stop at least 3 minutes after shutdown to restart? Stop at least 3 minutes after shutting down to start again 器2 䀀 ᅵ皥 䖒皦즠Ʋ煔क़ 㲈Ʋ 䌁皦 ᮔDž༬皧煞क़Ѐ 呄ᠾ鹨់༹皧 ࠄ 00령ꐱ댁珵뛐珵Љ 䕄ྦ 뤂ᐱ뚜珵 ᴴᏩ呄ᠾ퍘ᒥ 鹨់ᩄ ꋔྦ 瑉浥 巠皱㙲皦抐皱 巠皱 ੨皦柘皱 ᅵ皥 ب 巠皱㙲皦忈皱 ੨皦柘皱 즠Ʋǜ 勁皦즠Ʋب ǜ V / 펔B䌁皦 ᮔDž '鱤džၜ먢䇨珵呈ᠾ뤂ᐱ ⿇⬿먲僧ᐱ㥲ᐲ�僬㣢ᐲ ᠾ 랖僧і 識 �僬㣢
Customers frequently viewed

IWAYA DENKI Water Pump 25CJT0752
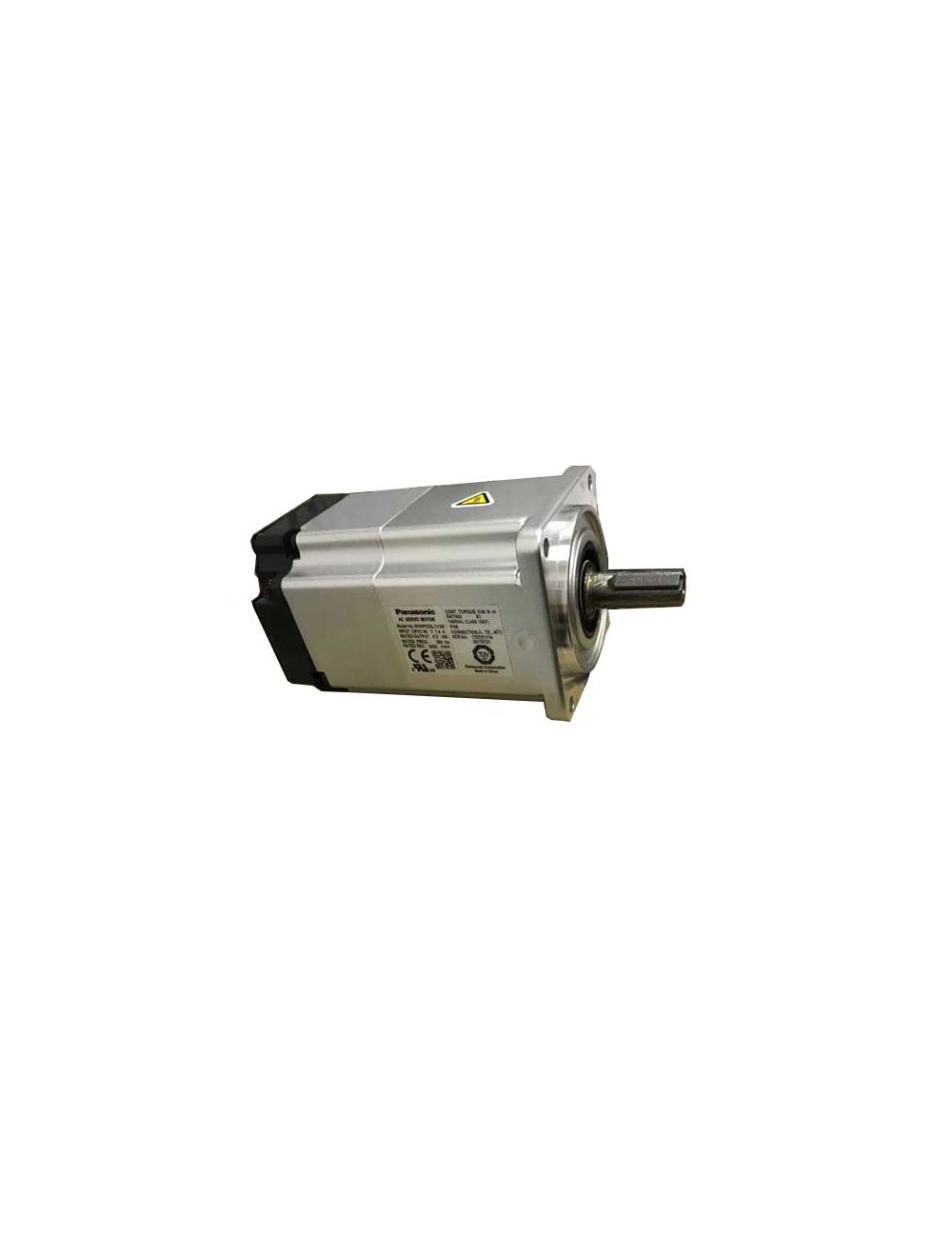
Panasonic Servo Motor MHMF022L1V2M

Honeywell Solenoid Valve VE4025B1045

ROTEN Mechanical Seal 8E5K-22-X

AirTAC Air Cylinder MAJ40X125-50

SMC Solenoid Valve SJ3160T-5CZD-C6-D

Hitachi Compressor BSD122DV-H3BR3