Talking about the installation method of condenser
For the vertical condenser, it should be placed on the basis of marking according to the drawing requirements, and the vertical line should be used to ensure the verticality of the installation. Pour the cement mortar in a correct way, and tighten the anchor bolts after it dries.
Horizontal condenser is usually installed together with the liquid receiver, the condenser is on the top and the liquid receiver is on the bottom. The condenser is fixed on the bracket 1 with screws. The bracket is generally made of concrete and equipped with semi-circular skids, which are calibrated with a spirit level. The horizontal tolerance is slightly inclined to the drain end.
The cooling water pipe of the condenser should enter from the lower part of the end cover and discharge from the upper part. The refrigerant enters from the upper end and flows out from the lower end. In this way, on the one hand, it can ensure that the heat transfer tubes in the entire condenser are filled with cooling water, and on the other hand, the heat exchange efficiency can be improved.
1. Installation of evaporator
When installing the water tank evaporator, first make the foundation with concrete, and put the asphalt treated skid on the foundation. The length of the skid is the same as the width of the water tank, and the quantity depends on the quality of the water tank and the evaporator. Then place the water tank on the skid, and then hoist the evaporator in the water tank and fix it.
A heat insulation layer is laid around the water tank, and the top of the tank is covered with this cover plate. The installation of the horizontal evaporator is similar to that of the horizontal condenser. An arc-shaped skid with the same thickness as the insulation layer and treated with asphalt soaking is placed on the support, and then the insulation layer is laid on the outside of the evaporator.
2. Installation of auxiliary equipment
In the refrigeration device, auxiliary equipment includes a liquid receiver, an oil separator, an intercooler, a vent, a gas-liquid separator and a filter. The installation of these devices has their own technical requirements. For larger equipment, shim irons should be placed under the base of the container and poured in cement mortar. After solidification, the anchor bolts should be tightened.
The principle of installation and takeover
The computer room should be spacious and the air should be unblocked. If necessary, an exhaust fan should be installed on the wall to enhance the ventilation of the computer room. Under the premise of ensuring the operating position of the operator and the necessary overhaul position, the equipment should be as close as possible to reduce the length of the pipeline to reduce the flow of negative force and cooling loss in the pipeline.
Each equipment should be kept away from heat sources. The electric motor of the unit shall be powered by a dedicated line. The cooling water pipe should also be dedicated to supply water. The laying of water pipes should take into account that the water in the condenser and water pump pipes can be drained in winter to avoid freezing and cracking of the condenser or water pump pipes.
Because the entire set of equipment has undergone an operation test before leaving the factory and has been filled with refrigerant, users generally do not need to disassemble and inspect the entire set of equipment or its components.
The position of the instrument panel of the unit should be easy to operate and observe. The installation of the condenser should be higher than that of the receiver to facilitate the discharge of the condenser.
The inner wall of the connecting pipe should be kept clean and dry without any other impurities. The piping layout should be correct, reasonable and beautiful, and minimize elbows. For Freon refrigeration systems, the smooth return of lubricating oil to the compressor should also be considered.
The insulation layer of the pipe wrapping should be carried out after the system leaks and confirms that there is no leakage.
Three, pipeline installation
The pipes in the refrigeration device include refrigerant pipes, cooling water pipes, refrigerant water refrigerant pipes, and the like. The correct design, layout and installation of the pipeline are directly related to the operational stability and economy of the refrigeration system.
The pipe diameter of each pipeline should be equipped according to the product specification or equipment requirements, and should not be changed randomly.
Freon pipes can be copper pipes or seamless steel pipes. When the pipe diameter is larger, seamless steel pipe is used, and the connection method is the same as that of the ammonia pipeline. When the pipe diameter is small, copper pipes are mostly used.
The copper pipe can be filled and cleaned with carbon tetrachloride solution before installation. Such as the residue of oxide scale and other dirt in the pipe,
can be pickled with the sulfuric acid solution of (, and then rinsed with cold water, and then with ((sodium carbonate solution for neutralization, after rinse with cold water and blow dry, seal it for later use.
The connection of the copper pipe can adopt silver brazing or copper brazing. The soldering temperature of silver brazing is lower and the solder has good fluidity. Copper brazing has high welding strength and low price, but because of the high temperature required for welding, mechanical oxidation impurities are easily generated during welding.
Tubes with the same diameter are mostly inserted with bulging and connected by brazing. The pipes of the ammonia refrigeration system must be seamless steel pipes, and not copper pipes or other non-ferrous metal pipes.
The inner wall of the pipe must be cleaned and dried before installation. For pipes with larger pipe diameters, a wire brush can be used to drag the pipe back and forth, and then blow it away with air. For small diameter pipes, a clean white cloth can be soaked with carbon tetrachloride liquid to scrub the inner wall of the pipe. It can also be filled with carbon tetrachloride night body, about, and then poured out, and then the pipe is blown dry and sealed for later use.
Ammonia pipeline connection generally uses arc welding. When the steel pipe is butted, the pipe mouth should be processed into proper groove in advance, and then welded with low-carbon steel electrode. The diameter of the electrode is selected according to the thickness of the pipe wall. Flange connection can be used for pipe connection where disassembly and maintenance are required.
When connecting in this way, the vertical deviation between the flange sealing surface and the pipe axis is not allowed to exceed -. The two joint surfaces are sealed with asbestos rubber gaskets coated with butter or graphite and oil mixed sealant. The thickness of the gasket is- between. The elbow required in the pipeline can be hot bending or cold bending.
Cold bending is suitable for small diameter pipes and must be bent with a special pipe bender. Hot bending requires heating the tube. If the bending radius is between -.times the pipe diameter, in order to prevent the pipe from bending, the sand filling method must be used for bending, and the inner wall of the pipe must be carefully sanded after the bending. The cooling water and refrigerant water pipelines generally use seamless steel pipes, welded steel pipes or galvanized steel pipes. Its connection method can adopt electric welding connection flange connection or threaded connection. When the thread is connected, first squeeze the tube out of the thread of the tube to remove oil and other impurities, apply a layer of paste sealant made of glycerin and alumina on the thread, and then wind fine linen or poly four The vinyl fluoride film, after , tighten it with a union. When the pipeline is above, the threaded connection method is generally not used.
Refrigerant water pipes generally use seamless steel pipes and are connected by copper brazing or tin brazing.
After all the pipelines are installed, use nitrogen or dry air for air tightness test. The size of the test pressure should be determined according to the pressure that the pipeline will bear during actual work. If leakage is found, repair welding and other measures should be taken. Pay attention to repair welding: it is not allowed to carry out under pressure in the pipe; the repair welding part needs to carefully remove the welding slag and rust layer, and wipe the surface with sandpaper; the steel pipe is not allowed to use brazing to repair leakage; the original copper brazing leakage The points can be repaired by silver brazing, but the missing points of the original silver brazing are not allowed to be repaired by copper brazing; the number of weld repairs should not exceed one, otherwise it should be cut off or re-welded.
IV. Precautions for pipe installation
Before installing the pipeline, the dirt, sand, rust, welding slag and oxide scale in the pipeline must be removed and kept dry.
The arrangement of pipelines should meet the requirements of the refrigeration process, and should take into account the convenience of construction, installation and operation management. The arrangement of the pipeline should not hinder the operation and operation management of the compressor and other equipment, nor hinder the maintenance of the equipment and the opening of doors and windows.
There should be a suitable distance between the pipe and the wall and ceiling, and between the pipe and the pipe, so as to install the pipe hanger and bracket for the insulation layer. On the same elevation, if there are both low-temperature and high-temperature pipelines, the high-temperature pipelines should be arranged above the low-temperature pipelines and kept a proper distance.
When the pipe passes through the wall or ceiling, a casing pipe should be installed so that the pipe has room for expansion and contraction due to temperature changes. For low-temperature pipelines, consideration should also be given to leaving an insulation layer of sufficient thickness.
The suction and discharge pipes of the compressor should have a certain slope. In order to prevent the liquid and lubricating oil condensed from the refrigerant vapor in the pipeline from flowing back into the compressor after the compressor is stopped, causing the liquid hammer phenomenon at the second start, the horizontal pipe section of the exhaust pipe should have a slope that is inclined to refrigeration The direction of flow of the agent. For the horizontal section of the suction pipe section, the slope of the ammonia compressor should be inclined to the low-pressure circulation barrel or the gas-liquid separator. Freon compressors should have a slope inclined to the compressor to facilitate oil return.
Talking about the installation method of condenser
Recent related posts
08/15/2020
Talking about the installation method of condenser
For the vertical condenser, it should be placed on the basis of marking according to the drawing requirements, and the vertical line should be used to ensure the verticality of the installation.
08/15/2020
Summer chiller failure detection and solutions
The weather is getting hotter and hotter, and the industrial chillers of many factories ushered in the peak period of refrigeration. Frequent operation of refrigeration equipment is likely to have such and other small failures.
08/15/2020
Steps to determine the cause of the failure of the thermal expansion valve
1. When the refrigerant of the refrigeration system leaks completely, or there is no refrigerant flowing through the thermal expansion valve due to other reasons, the valve body of the thermal expansion valve will not be frosted.
08/15/2020
Solution to the condensing pressure of the chiller refrigeration system
1. The condenser of the chiller is dirty Computer room chillers generally use air-cooled condensers, which are composed of multiple sets of coils, and fins are added to the coils to increase the heat transfer area on the air side.
08/15/2020
Simple treatment method after the refrigeration system enters water
Since the chiller has a water system, there is a possibility that the refrigerant system may enter water when it is used improperly. Therefore, a process guide is formulated for the problem of water ingress
08/15/2020
Several methods to detect the quality of refrigerator compressor
The compressor is the heart of the refrigerator refrigeration system, and its quality directly affects the performance of the refrigerator. Therefore, in the process of detecting the quality of the refrigerator
08/15/2020
Selection knowledge of screw chiller
Screw chiller is a large-scale industrial refrigeration equipment. It is widely used in central air-conditioning and large-scale refrigeration industry. It plays an important role in refrigeration, cooling and cooling.
08/15/2020
Refrigeration methods and energy-saving methods of industrial refrigerators
Perhaps many friends are not very familiar with industrial refrigerators. In fact, this kind of equipment is aimed at refrigeration equipment in industrial production and can provide the most
08/15/2020
Reasons for the large difference in cooling of different refrigeration equipment
According to the analysis of the use environment, due to the differences in the cooling methods of the refrigeration equipment, enterprises need to carefully analyze the particularity of the use
08/15/2020
Precautions for the installation of refrigeration equipment
For large enterprises that need to use refrigeration equipment, due to the larger scale of the enterprise, the demand for refrigeration will also be greater. Therefore, when selecting and installing refrigeration equipment
Customers frequently viewed

IWAYA DENKI Water Pump 25CJT0752
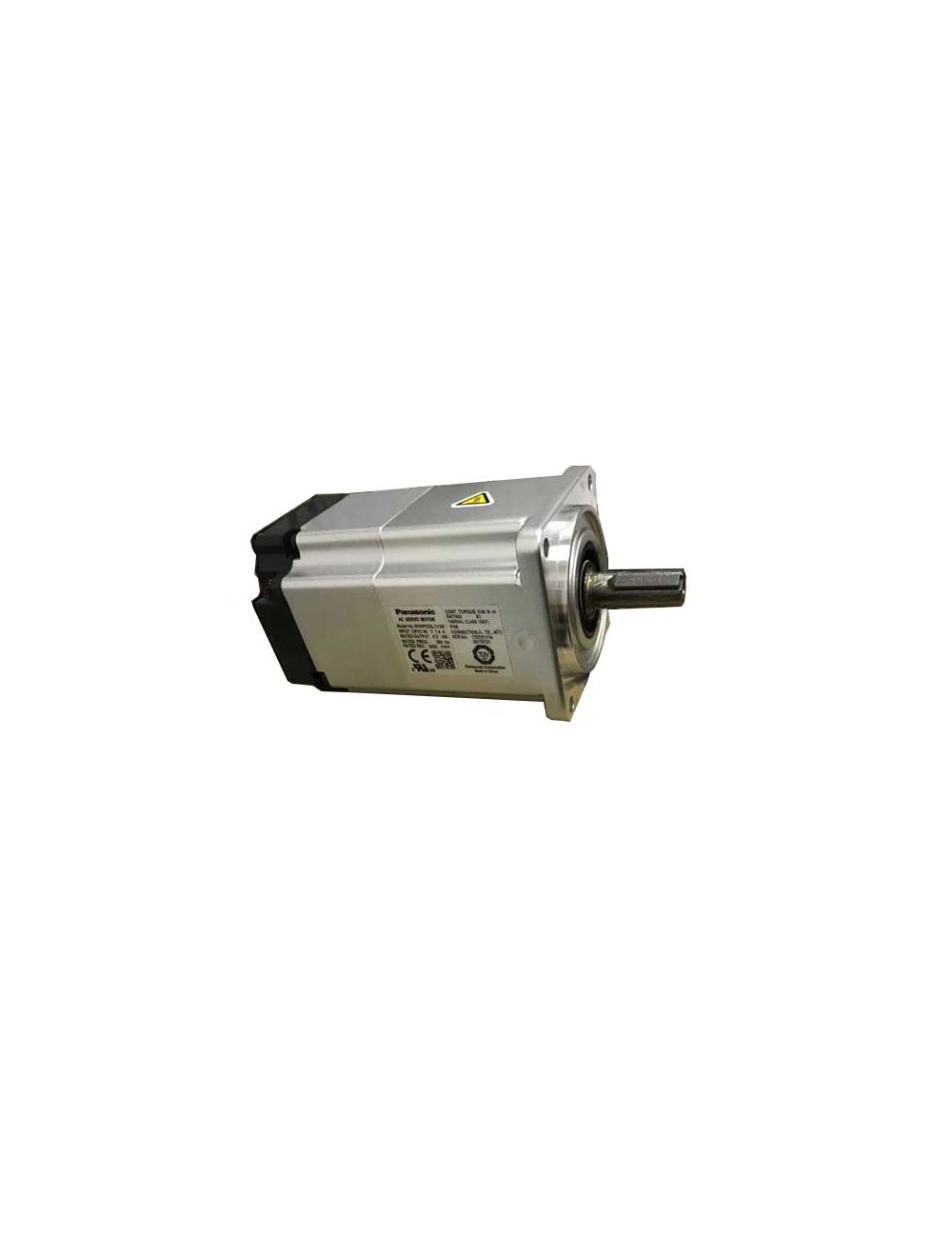
Panasonic Servo Motor MHMF022L1V2M

Honeywell Solenoid Valve VE4025B1045

ROTEN Mechanical Seal 8E5K-22-X

Mitsubishi Servo Motor HC103T-SX

MAHLE Filter KL1085
HONGFA Relay HFD3-5