The difference between oil cooler and other coolers
An oil cooler is a heat exchanger that uses air to cool hot fluid. Like other coolers, rust scale will appear. The rust scale appears mainly because the cooling water contains a large amount of calcium, magnesium ions and acid carbonates. When the cooling water flows through the metal surface, carbonates will be produced; except for this dissolution The oxygen in the cooling water will also cause metal corrosion to form rust. When it produces rust, the heat exchange effect will decrease. In severe cases, the tube will be blocked and the heat exchange effect will be lost. To achieve the cooling effect, it is necessary to spray cooling water on the shell. And as the deposits continue to increase, energy costs will increase, because as long as a very thin layer of scale will increase the operating costs of the scaled part of the equipment by more than 40%, the impact of scale on heat transfer is huge of.
One. Features:
1. The water-cooled oil cooler uses water as the medium to exchange heat with oil. The advantage is that the cooling effect is better, and it can meet the requirements of relatively low oil temperature (the oil temperature can be reduced to about 40 ℃, the disadvantage is that there must be a water source Place to use.
2. The air-cooled oil cooler uses air as the medium and oil for heat exchange. The advantage is that air is the cooling source, which is basically not limited to the place where it is used. It is environmentally friendly. The disadvantage is that it is affected by the ambient temperature and the temperature is higher. The oil temperature cannot be reduced to the ideal temperature (air cooling is generally difficult to reduce the oil temperature to only 5~10℃ higher than the ambient temperature).
2. Pay attention to the problem
The plate type or corrugated type should be determined according to the actual needs of the heat exchange occasion. If the flow rate is large and the pressure drop is small, the plate type with low resistance should be selected, otherwise, the plate type with large resistance should be selected. According to the fluid pressure and temperature, determine whether to choose a detachable type or a brazed type. When determining the plate type, it is not advisable to choose a plate with a single plate area that is too small, lest there are too many plates, the flow velocity between the plates is too small, and the heat transfer coefficient is too low. This problem should be paid more attention to for larger heat exchangers.
process refers to a set of parallel flow channels in the same flow direction of a medium in the plate heat exchanger, and the flow channel refers to the medium flow channel composed of two adjacent plates in the plate heat exchanger. Generally, several runners are connected in parallel or in series to form different combinations of cold and hot medium channels.
The process combination form should be calculated based on heat exchange and fluid resistance, and determined under the requirements of process conditions. Try to make the convective heat transfer coefficients in the cold and hot water channels equal or close to each other to get the best heat transfer effect. Because the convective heat transfer coefficient on both sides of the heat transfer surface is equal or close to the heat transfer coefficient to obtain a larger value. Although the flow velocity between the plates of the plate heat exchanger is not equal, the average flow velocity is still used in the calculation of heat exchange and fluid resistance. Because the "U"-shaped single-flow pipes are fixed on the compression plate, it is convenient to disassemble and assemble.
In the design and selection of plate heat exchangers, there are generally certain requirements for pressure drop, so it should be checked. If the check pressure drop exceeds the allowable pressure drop, the design selection calculation needs to be re-calculated until the process requirements are met.
Three, oil cooling performance
1. Wide heat transfer area: The heat transfer tube of this cooler adopts a copper tube threaded design, and its contact area is wide, so the heat transfer effect is higher than that of a normal smooth heat transfer tube.
2. Good heat transfer: This series of copper tubes are directly processed by spinning copper tubes to make the heat transfer tube integrated, so the heat transfer is good and reliable, and there is no solder joint falling off and poor heat transfer.
3. It can be suitable for large flow: the number of heat transfer tubes is reduced, the area of smooth oil is increased, and pressure loss can be prevented. It is equipped with a partition to guide the flow direction, which can produce a curved flow direction, increase the flow, and exert its effectiveness.
4. Good heat transfer tube: 99.9% pure copper with good thermal conductivity is used, which is a cooling tube suitable for heat dissipation.
5. No oil leakage: Because the plate tube and the body adopt an integrated design, it can avoid the trouble of water and oil mixing. At the same time, the air tightness test is really tight before leaving the factory, so it can achieve the purpose of leak prevention.
6. Easy assembly: The foot can be rotated freely in 360 degrees, and the direction and angle of the body can be changed at will. The foot can be directly welded to any position of the mother machine or oil tank through the foot, which is convenient and simple.
7. The spiral baffle guides the oil to flow uniformly and continuously in a spiral shape, which overcomes the dead angle of heat exchange caused by traditional baffle, with high heat exchange efficiency and low pressure loss.
8. There are two processes and four processes for water flow, with large flow (large lead of the deflector) and small flow (small lead of the deflector). There are various varieties to meet various requirements.
The difference between oil cooler and other coolers
Recent related posts
08/14/2020
The difference between oil cooler and other coolers
An oil cooler is a heat exchanger that uses air to cool hot fluid. Like other coolers, rust scale will appear. The rust scale appears mainly because the cooling water contains a large amount of calcium, magnesium ions and acid carbonates.
08/14/2020
The difference between independent and non-independent refrigeration units
The cold storage is a special place dedicated to refrigeration, and now it is mainly used to keep food fresh. With the increasing requirements for the freshness of food, the use of cold storage is gradually increasing.
08/14/2020
The detection of the power supply voltage of the chiller
Industrial chiller units are widely used. Where there is industry, chiller equipment is required, such as: chemical chillers, electroplating chillers, food chillers, electronic processing chillers, mold chillers, printing chillers, etc.,
08/14/2020
The correct way to open the refrigerated truck for summer maintenance
With the advent of summer, the maintenance of refrigerated trucks is becoming more and more important. In order to prevent the high temperature in summer from damaging the surface of the refrigerated truck,
08/14/2020
Specification for selection and installation of refrigeration piping parts for chillers
The accessories of the refrigeration pipeline of the chiller mainly include various valves and connectors. Depending on the refrigeration system, the chiller's request for piping accessories is also different.
08/14/2020
Several details in the cold storage installation process
Hello, dear readers and friends, today the editor of okmarts.com will briefly introduce you to several details of the cold storage installation process.
08/14/2020
Selection requirements for cold storage refrigerants
The nature of the refrigerant will directly affect the type, structure, size and operating characteristics of the refrigerator, as well as the form, equipment structure, and economic and technical performance of the refrigeration cycle.
08/14/2020
Reasons for internal protection of industrial chiller compressors
There is a thermal switch inside some compressors. The function of this switch is to disconnect the power supply line to the compressor motor when the temperature of the compressor exceeds the set value.
08/14/2020
Protection preparation before cold storage installation
Once the cold storage is installed or used improperly, it is very likely to affect the smooth application of the cold storage.
08/14/2020
Precautions for refrigeration piping
The refrigeration industry is now in a period of rapid development. In order to facilitate the refrigeration installation of refrigeration equipment, here is the refrigeration equipment manufacturer to share with you the successful experience accumulated by our technicians.
Customers frequently viewed

IWAYA DENKI Water Pump 25CJT0752
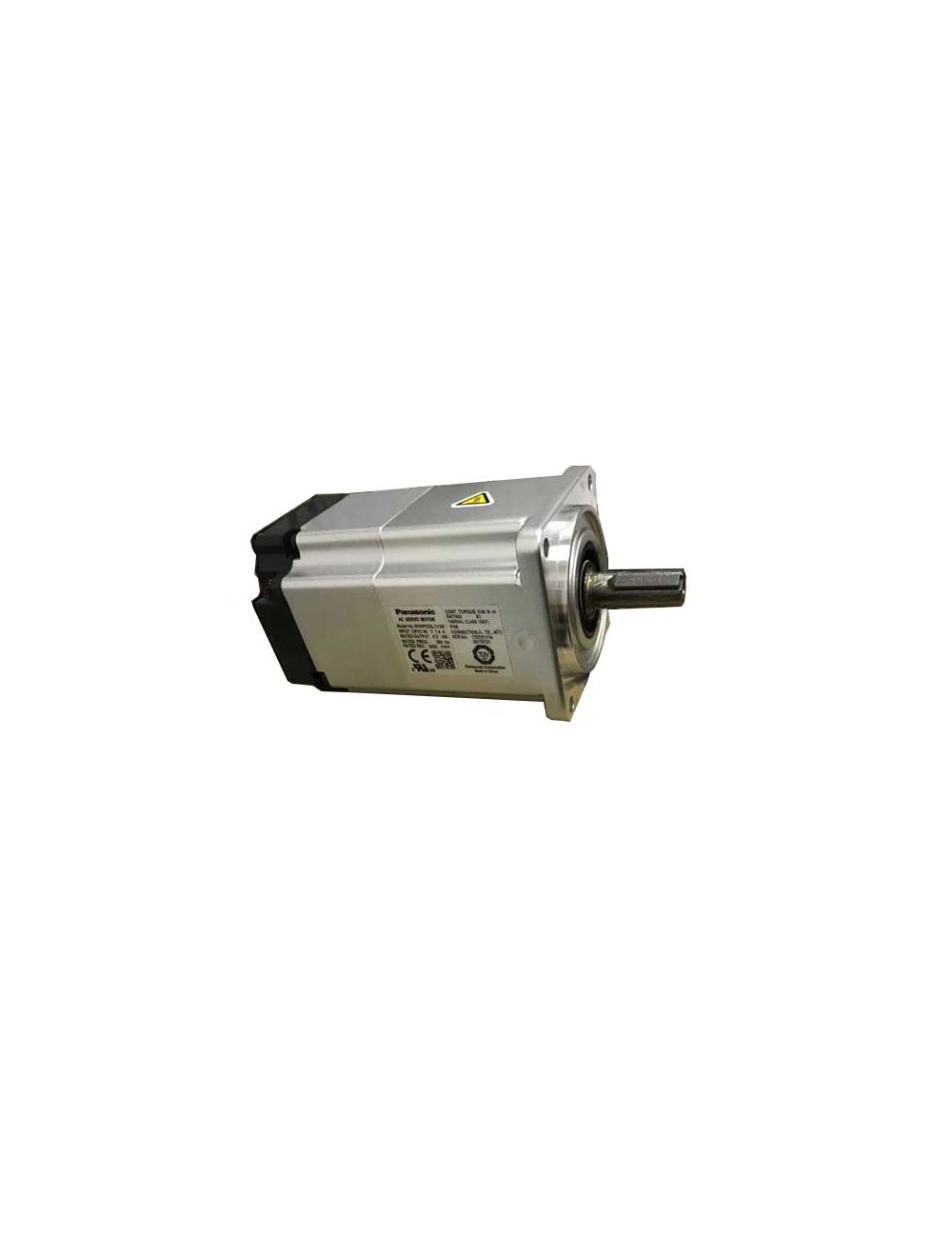
Panasonic Servo Motor MHMF022L1V2M

Honeywell Solenoid Valve VE4025B1045

ROTEN Mechanical Seal 8E5K-22-X

NMB-MAT Fan 3615ML-04W-B76

KCL Vane Pump VQ15-23-F-RLR-02

Ebmpapst Fan W2E208-BA20-51

Protechnic Fan MGT4024XB-R10

Nedfon Fan DKT20-7.5KW