Brief analysis of the structure and working principle of the oil separation core and the cause of failure
There is an important part of the oil and gas separator of the screw air compressor called the oil separation core. Many customers are very confused about the burning of the oil separation core. Now let's understand its working principle and analyze the cause of the oil separation core burning.
The structure and working principle of the air compressor oil separation core:
Brief analysis of the structure and working principle of the oil separation core and the cause of failure
The oil separation core in the oil and gas separator separates the oil and gas, allows the oil to return to the internal circulation of the machine, and allows the gas to be discharged for the user. The oil and gas mixture enters the oil and gas separation tank and hits the curved surface, the flow rate is greatly reduced, the flow direction is changed, and large oil droplets are formed. Because they are heavier, the large oil droplets enter the bottom of the tank. The remaining small part of the oil is separated when flowing through the separation element and deposited on the bottom of the filter element. An oil return pipe from the bottom of the separation core is connected back to the compressor inlet; due to the pressure difference, the oil accumulated at the bottom of the separation core flows back to the compressor inlet. The oil return pipe has a sight glass and a throttle hole (front filter) Ensure stable oil return.
The filter element of the air compressor oil separator is made of multiple layers of fine glass fiber. The misty oil and gas contained in the compressed air can be almost completely filtered out after passing through the oil separator, below 3ppm. Under normal operation, the pollution degree of the lubricating oil and the surrounding environment has a great impact on its life. If the environmental pollution is very serious, you can consider installing a pre-air filter; the outlet of the oil separator is equipped with a pressure maintenance valve to compress air The machine is led out from here to the rear cooler. There are safety valves and relief valves connected to the outlet of the oil separator. The oil filtered by the oil separator core is concentrated in the small circular groove in the center of the bottom, and then flows back to the bearing end of the body through an oil return pipe, which can prevent the filtered lubricating oil from being discharged with the air.
Brief analysis of the structure and working principle of the oil separation core and the cause of failure
In the process of using, you will encounter different failure problems, and the burning of the oil core is one of them. The oil separation core burnt failure is actually the oil separation core being ignited. What are the main reasons for this?
1. The oil content in the air pipe increases.
2. Check whether the oil pressure is too high. Generally, the screw air compressor has a pressure gauge before the filter element. When the pressure difference between the pressure gauge before the filter element and the air supply pressure gauge reaches 0.08MPa, the oil separation element is replaced.
3. Whether the current increases.
4. Open flame caused by electrostatic discharge. Check whether the grounding of the air compressor is normal, and whether the oil and gas barrel is connected to the ground of the machine. When replacing the oil separator core, be sure to pay attention to the static conductive nail in the gasket on the oil separator core. That nail is grounded to the ground to remove all the static electricity generated when the oil is inserted in the oil separator core.
5. The quality of the oil is caused by poor oil quality, carbon deposits are generated, the safety valve is blocked by carbon deposits, and the internal pressure is too high, causing the oil to explode.
Note: 1. When the air compressor has been used for a period of time, or when it is low in winter, before starting the machine again, add a small amount of lubricating oil to the main engine so that there is lubricating oil and cooling when the main engine starts.
2. Pay attention to the exhaust temperature of the air compressor during daily operation. If the exhaust temperature of the machine is too high for a long time, find out the cause of the high temperature and solve the problem.
Brief analysis of the structure and working principle of the oil separation core and the cause of failure
Recent related posts
09/01/2020
Brief analysis of the structure and working principle of the oil separation core and the cause of failure
There is an important part of the oil and gas separator of the screw air compressor called the oil separation core. Many customers are very confused about the burning of the oil separation core.
09/01/2020
Application of compressed air in sandblasting equipment
For a long time, the compressed air produced by the air compressor unit is not only widely used in machine tool equipment in the machining industry, but also widely used in the metal surface processing industry.
09/01/2020
Analysis of three states of mechanical lubrication
There are three types of lubrication: full film lubrication, boundary lubrication, and mixed lubrication. They are in three different states, but they all rely on lubricating oil to lubricate and resist wear.
09/01/2020
Analysis of System Energy Saving Scheme of Centrifugal Compressor Application Enterprise
If the level of energy consumption cannot be significantly reduced, the current resources and environment may not be able to bear it. Therefore, "energy saving and emission reduction" made the strongest voice at the "two sessions"
09/01/2020
Analysis of heat recovery of oil-free air compressor
1.The working principle of oil-free air compressor cooling The air enters the first-stage low-pressure rotor pressurization and intercooler cooling through the filter, and then enters the second-stage high-pressure rotor pressurization and aftercooler
08/31/2020
How to achieve zero consumption of compressed air for drainage
This article discusses the working principle of the compressed air zero-consumption automatic steam trap, and gives the most marketable accessory installation sample structure, and the actual energy-saving effect achieved in the actual application of the enterprise.
08/31/2020
Talk about the artisan spirit of the compressor industry
The compressor industry is an important part of the manufacturing industry. If we want to do a good job in this industry, we need people to operate. The human factor is the key, especially the first-line skilled workers with certain skills. After all, they are the main force of production... ..
08/31/2020
Facing the current dilemma in the air compressor industry, how to break through
2019 is different from any previous year. In 2019, as the President of the United States raised aloft; Make the United States great again; the flag, the trade sanctions against China are also increasing, making our future full of uncertainty.
08/31/2020
Play screw technology to the extreme-re-disc medical vacuum screw technology
The earliest history of mankind's vacuum can be traced back to the 6th century BC. The smelting furnace and alchemy furnace's blast design utilizes negative pressure suction and pressurized exhaust.
08/31/2020
Market application and prospect analysis of air compressor waste heat recovery
Background With the rapid development of industry and economy, people's demand for energy is also increasing day by day. With the endless exploitation of human beings, the reserves of fossil fuels are decreasing day by day, and the world energy crisis is increasing day by day. Subsequently,
Customers frequently viewed

IWAYA DENKI Water Pump 25CJT0752
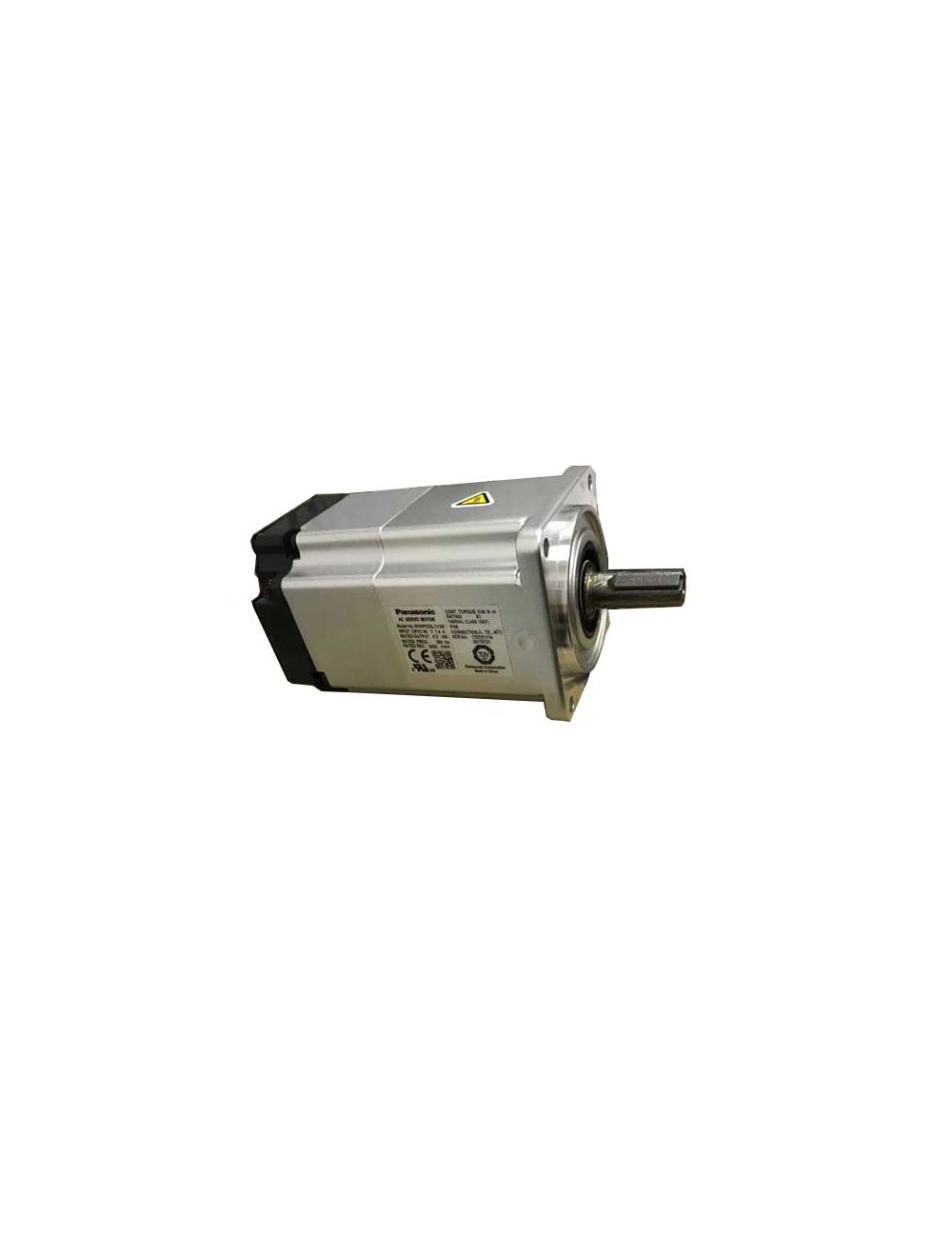
Panasonic Servo Motor MHMF022L1V2M

Honeywell Solenoid Valve VE4025B1045

ROTEN Mechanical Seal 8E5K-22-X

Siemens Contactor 3RT2017-2BW42

PIZZATO Switch HX BEE1-KSMH15